
Application of precision casting in fluid chemical industry
Precision casting is mainly used to produce chemical equipment components that are corrosion-resistant, high-temperature resistant, high-pressure resistant, and structurally complex, such as pump valves, pipeline fittings, reactor components, tower components, etc. Its core is to ensure stable operation of parts under harsh working conditions such as strong acid, strong alkali, high temperature, and high pressure through precise control of the casting process, while meeting the extremely high requirements of the chemical industry for safety, reliability, and corrosion resistance.
Our achievements in the field of fluid chemistry
We mainly provide stainless steel ball valves, check valve accessories, chemical centrifugal pump accessories, impellers, seamless elbows, tees, supports, pipe boxes, etc. to some large fluid petrochemical companies in China. I hope to cooperate with excellent fluid chemical companies from various countries and create excellent results together.
Our capabilities in the field of fluid chemistry
1.Due to the special requirements of chemical fluids, material corrosion resistance is given priority. We mainly use corrosion-resistant materials such as stainless steel (such as 304, 316L, 904L), nickel based alloys (such as Inconel 625), titanium alloys, duplex steels, etc. Some working conditions require the use of special alloys such as Hastelloy and Monel. For example, the valve used to handle concentrated hydrochloric acid should be made of Hastelloy C-276, as it has excellent corrosion resistance to wet chlorine, oxidizing acids, and mixed acids.
2. Complex flow channels (such as twisted blades of multi-stage pump impellers), thin-walled structures (such as heat exchanger tube plates), or composite parts with lining (such as steel substrate+corrosion-resistant alloy lining) need to be formed. Accuracy achieved: The tolerance level is usually CT6-CT9, with a surface roughness Ra ≤ 6.3 μ m. Important sealing surfaces require subsequent grinding (such as valve sealing surface roughness Ra ≤ 0.8 μ m).
3. We conduct strict quality control and non-destructive testing: 100% penetrant testing (PT) or magnetic particle testing (MT) screen for surface defects, and important parts require radiographic testing (RT) or ultrasonic testing (UT). Pump and valve components are subjected to water/air pressure tests (such as API 598 standard), with a test pressure of 1.5 times the working pressure and holding for 30 minutes without leakage. In intergranular corrosion testing, stainless steel parts need to pass intergranular corrosion testing according to standards such as ASTM A262 to ensure that intergranular corrosion does not occur in chemical media.
Parameter
Category |
Parameters |
Casting Materials |
Common materials: Carbon steel, stainless steel, alloy |
Material weight range: 0.003 kg - 110 kg |
|
Casting Dimensions |
Maximum casting size: Ø600mmX800mm |
Minimum casting size: 5 mm x 5 mm x 5 mm |
|
Casting wall thickness: 1 mm - 20 mm |
|
Casting Precision |
Dimensional tolerance: ±0.05 mm - ±0.2 mm (depending on casting size) |
Surface roughness: Ra 3.2 µm -6.3 µm |
|
Production Capacity |
Annual output: 600 tons |
Maximum single piece weight: 110 kg |
|
Minimum single piece weight: 3 grams |
|
Mold materials: Wax molds, ceramic molds |
|
Casting Process |
Mold types: Precision wax mold casting |
Pouring methods: Gravity casting, vacuum casting |
|
Heat Treatment Capability |
Heat treatment processes: Normalizing, annealing, quenching, tempering |
Treatment furnace temperature range: 600℃ - 1100℃ |
|
Post-Processing |
Surface treatment: Polishing, sandblasting, machining, painting, hot-dip galvanizing, powder coating |
Instant inquiry
Products in the pump and valve field are mostly shaped parts, and have high sealing and pressure resistance requirements, so they are more suitable for stainless steel precision casting technology.
Technological Process
Investment casting is a manufacturing process in which a liquid material is poured into a ceramic mold, which contains a hollow cavity of the desired shape, and then allowed to solidify. The solidified part is the casting, which is broken away from the ceramic mold to complete the process. The steps within the investment casting process are as follows:
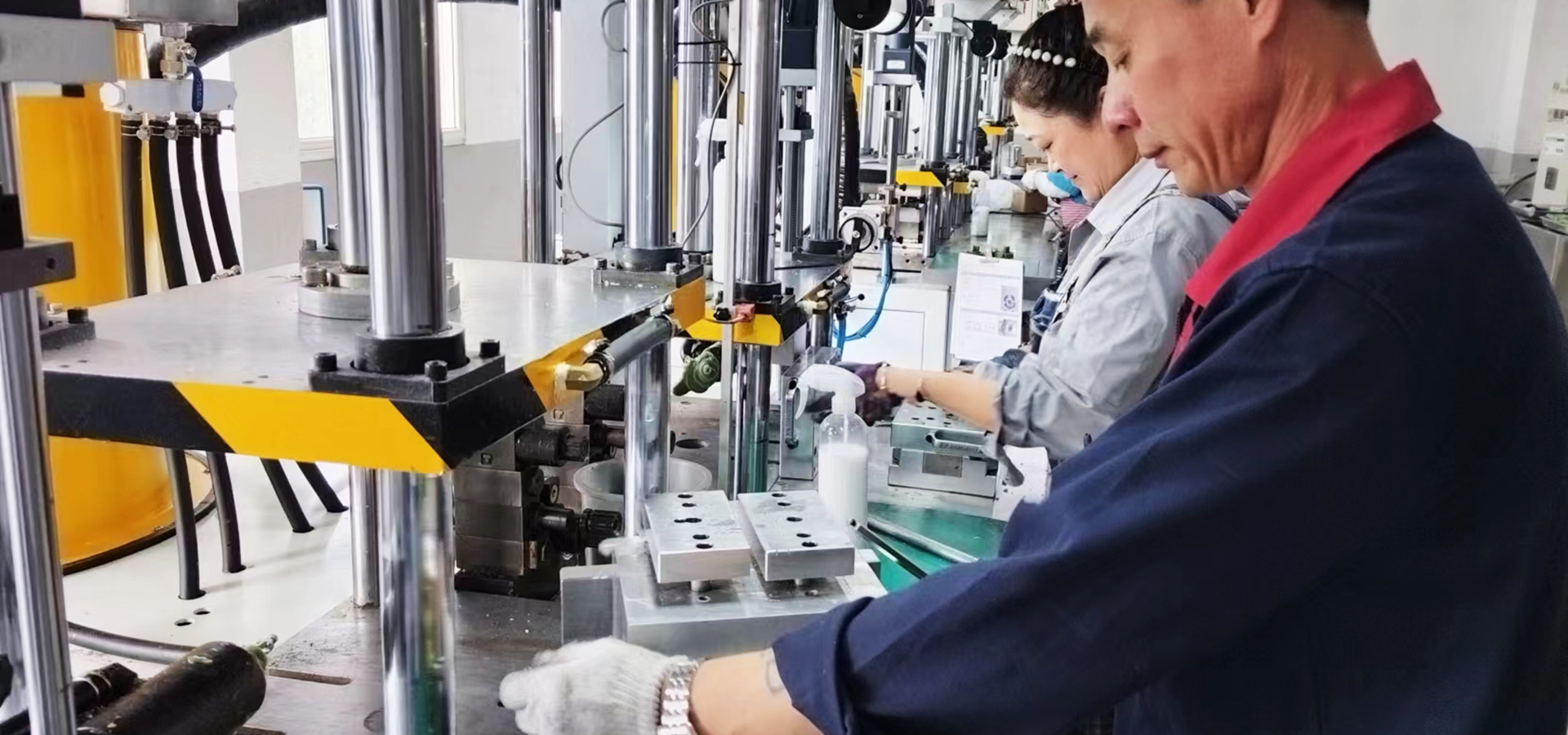
01
Wax Injection
Injection of medium-temperature wax (60-65°C) into metal molds under 0.5-0.7 MPa pressure, with a dwell time of 20-30 seconds.
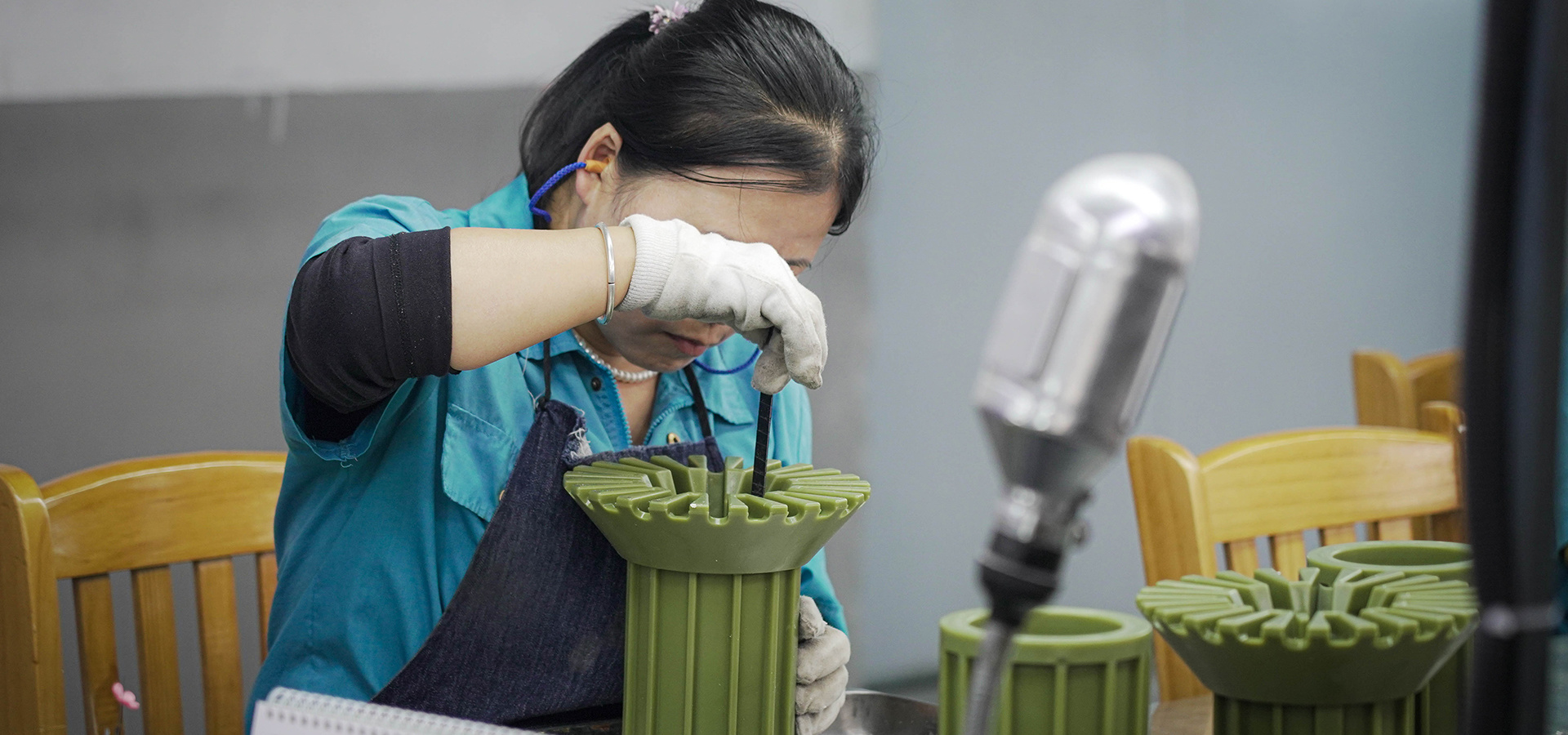
02
Wax Pattern Trimming
Removal of flash from wax pattern parting lines with precision ±0.1 mm, using hot knives (70-90°C)
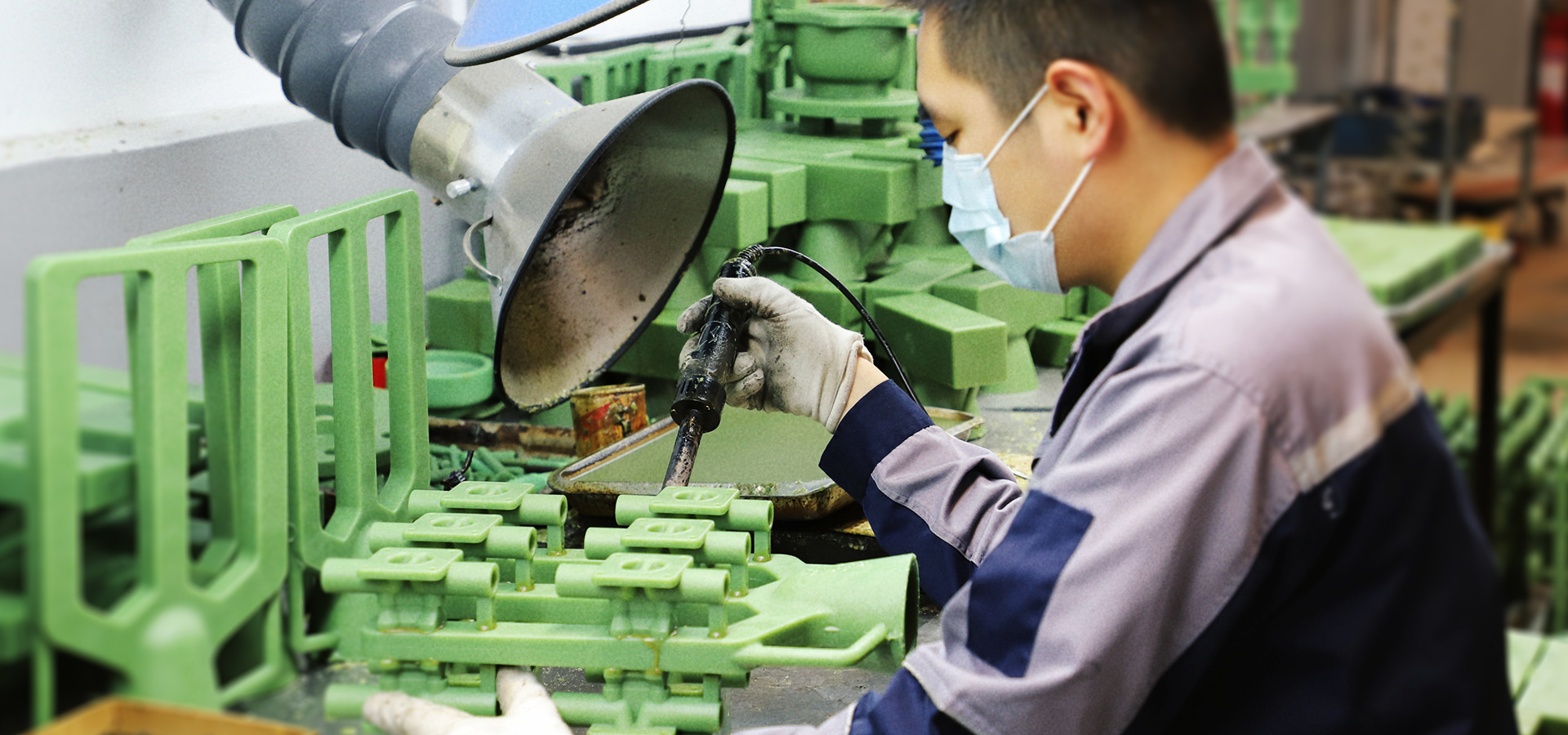
03
Cluster Assembly
Welding wax patterns to a central sprue, with cluster weight ≤15 kg, pattern spacing ≥8 mm, and pouring angle of 25-30°.
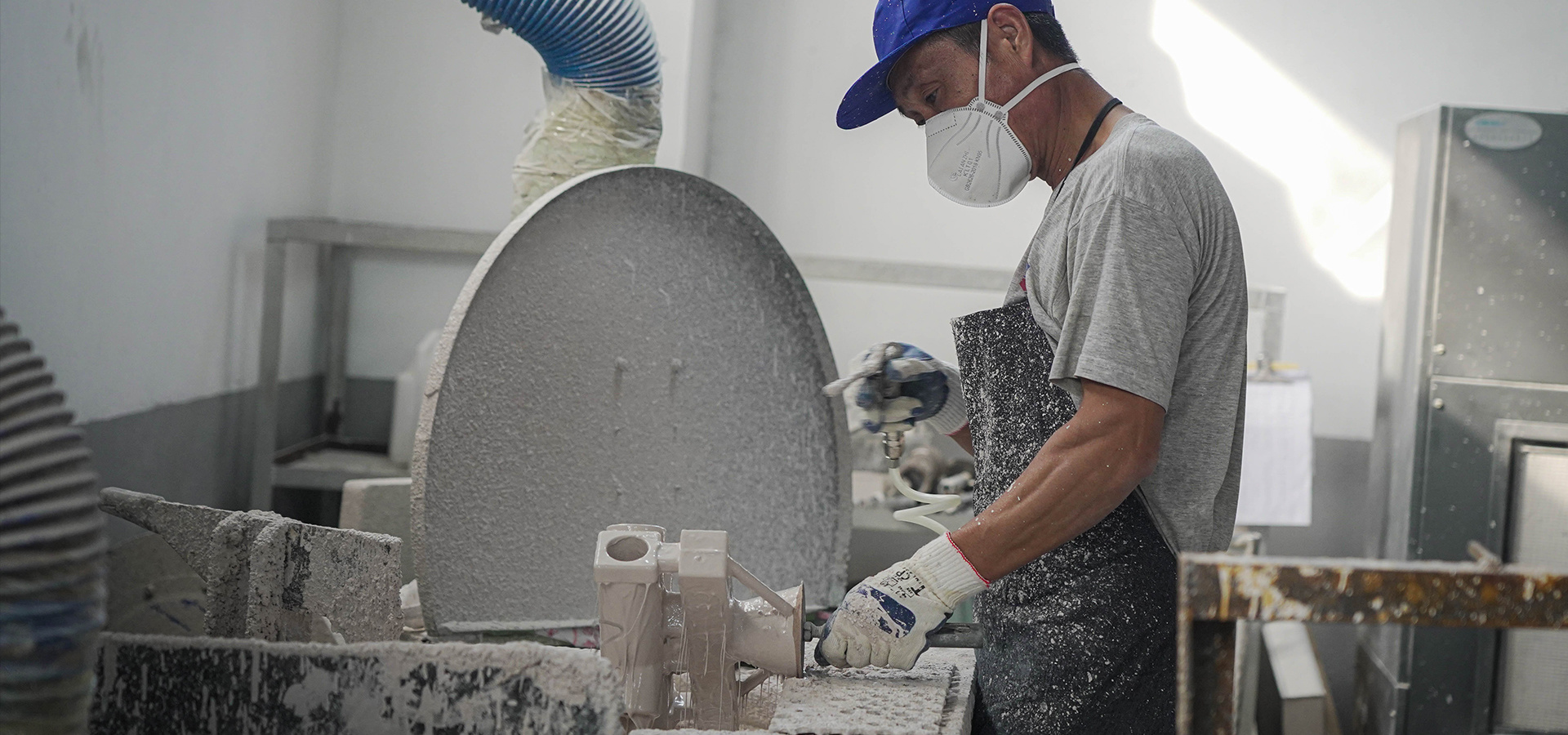
04
Primary Coating
Silica sol (SiO₂ 20%) + zircon flour (ZrO₂ 80%), 320-mesh,viscosity 42-45 seconds (#4 Zahn cup), coating thickness 0.3-0.5 mm.
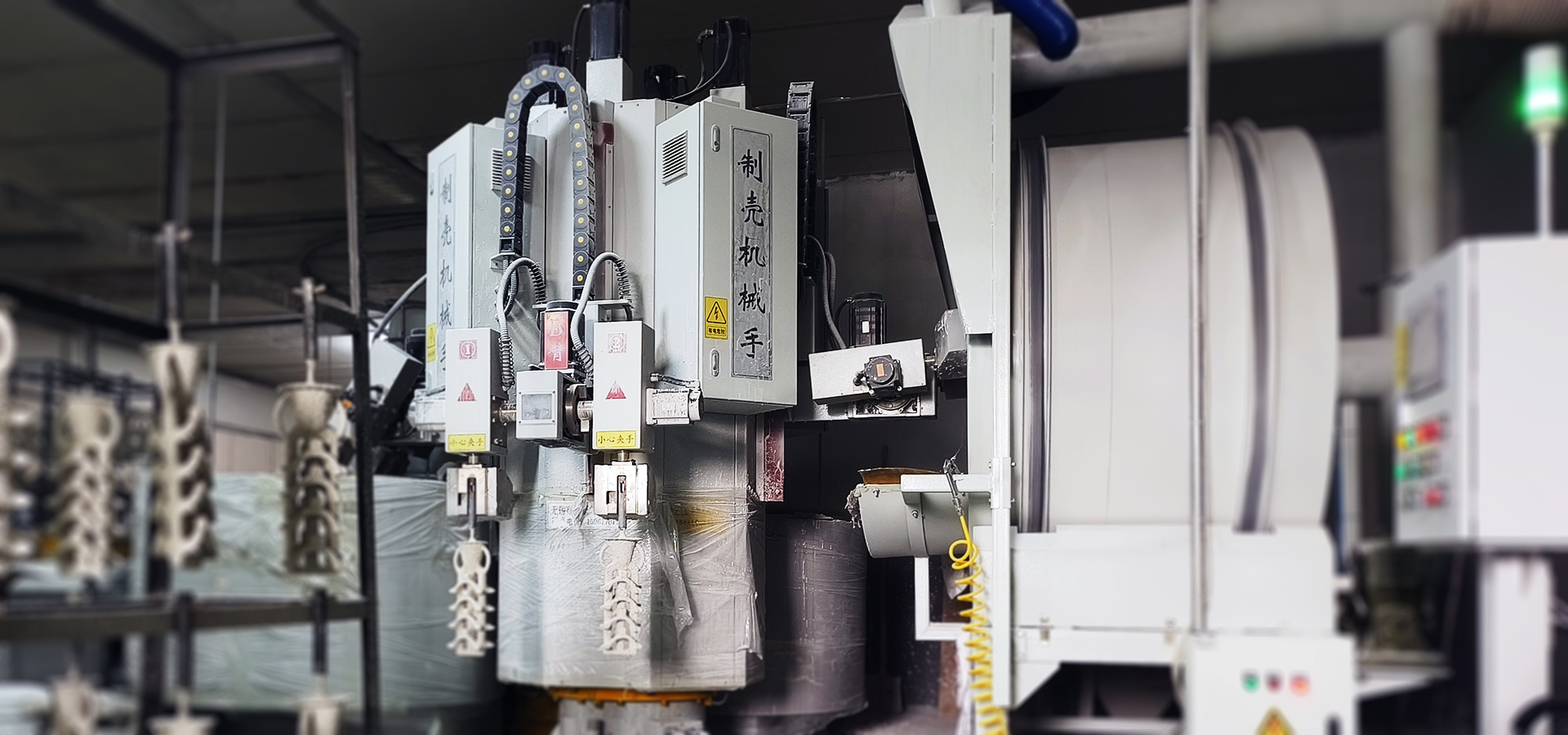
05
Backup
Quartz sand, 80~120-mesh 、30~60-mesh 、16~30-mesh chamotte sand stuccoing, total shell thickness 6-8 mm, green strength ≥4 MPa.
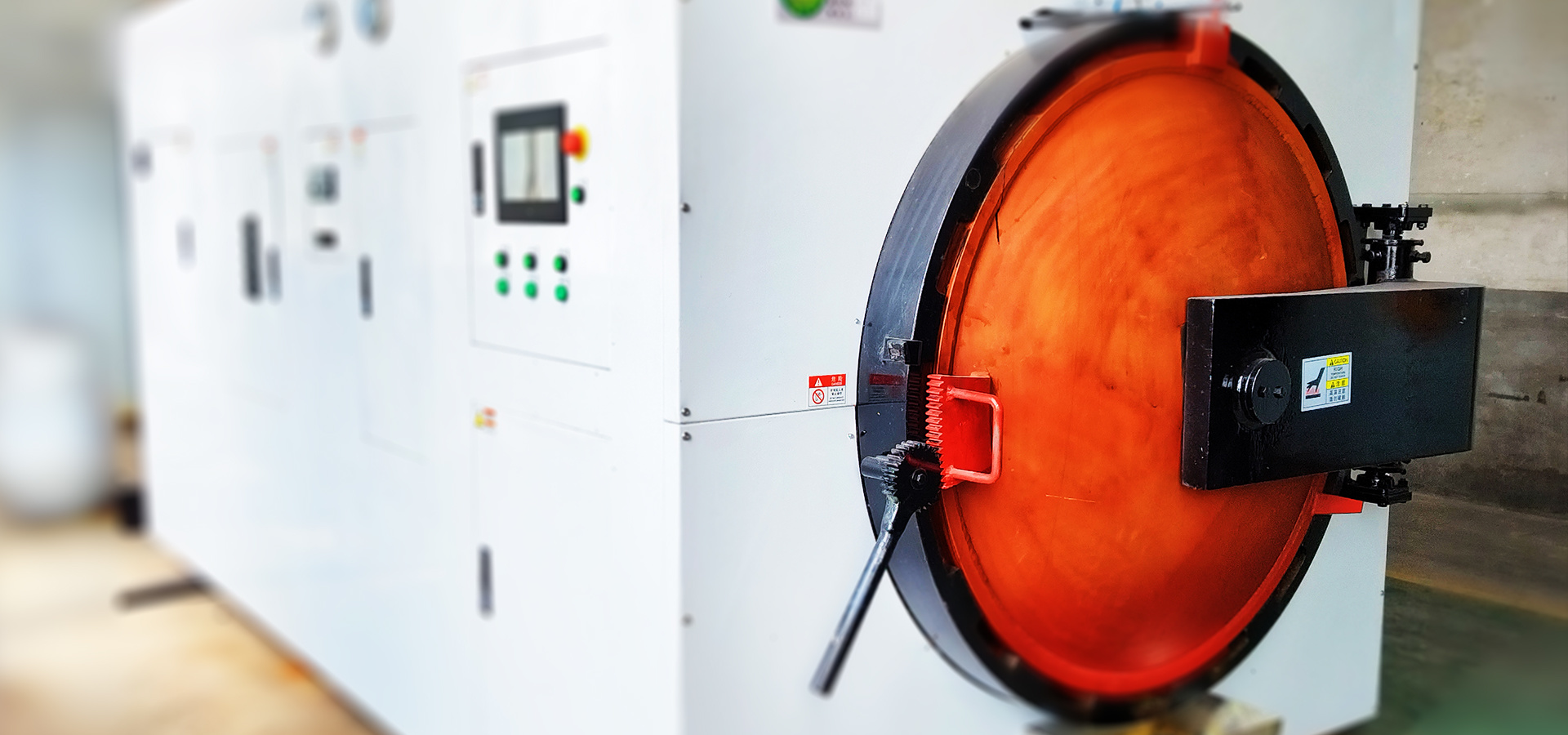
06
Dewaxing
High-pressure steam dewaxing (0.6-0.8 MPa, 150-170°C), residual wax ≤0.3%, shell breakage rate <0.5%.
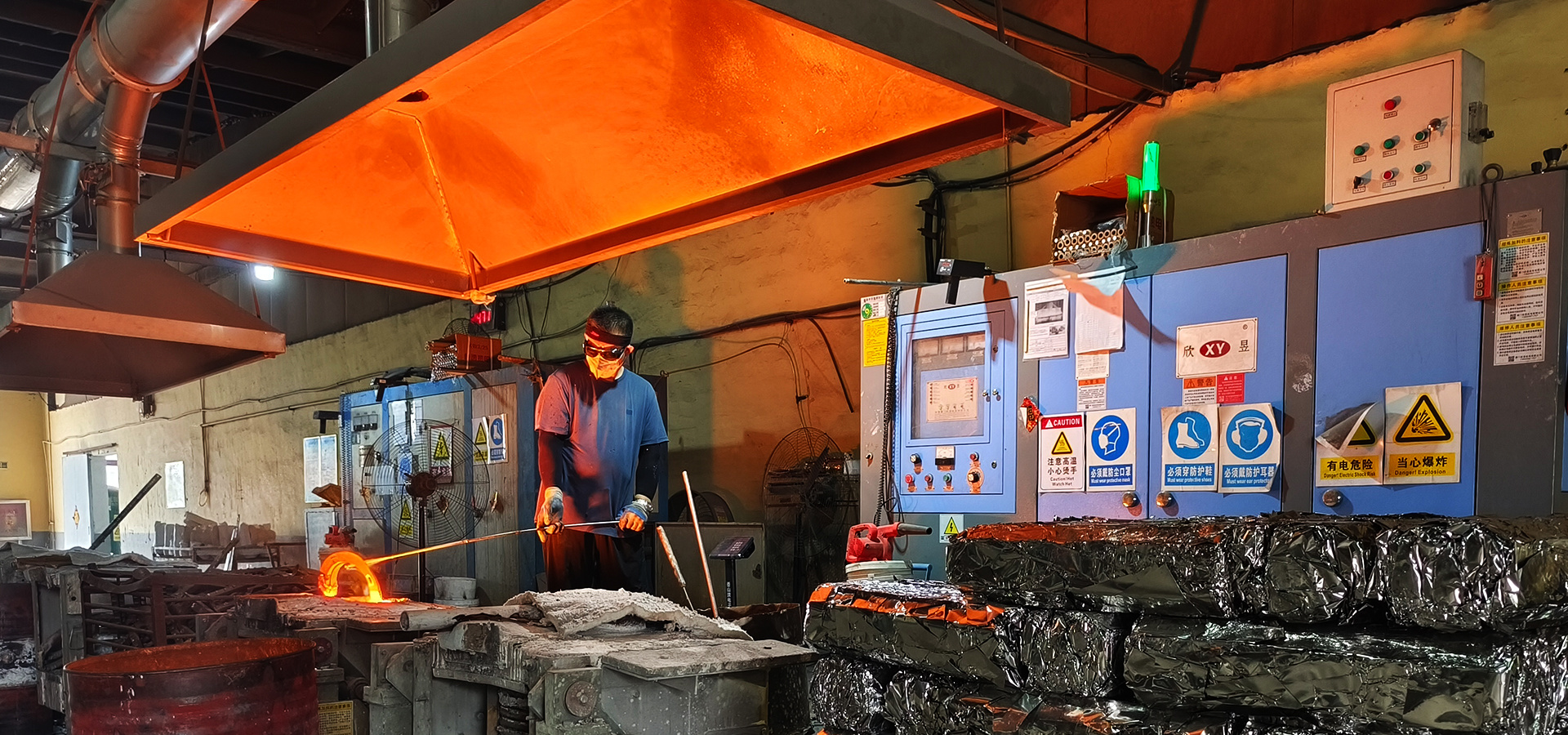
07
Pouring
Gravity casting with preheated molds (1000-1200°C), pouring rate 0.8-1.2 kg/s, solidification cooling rate 50-100°C/min.
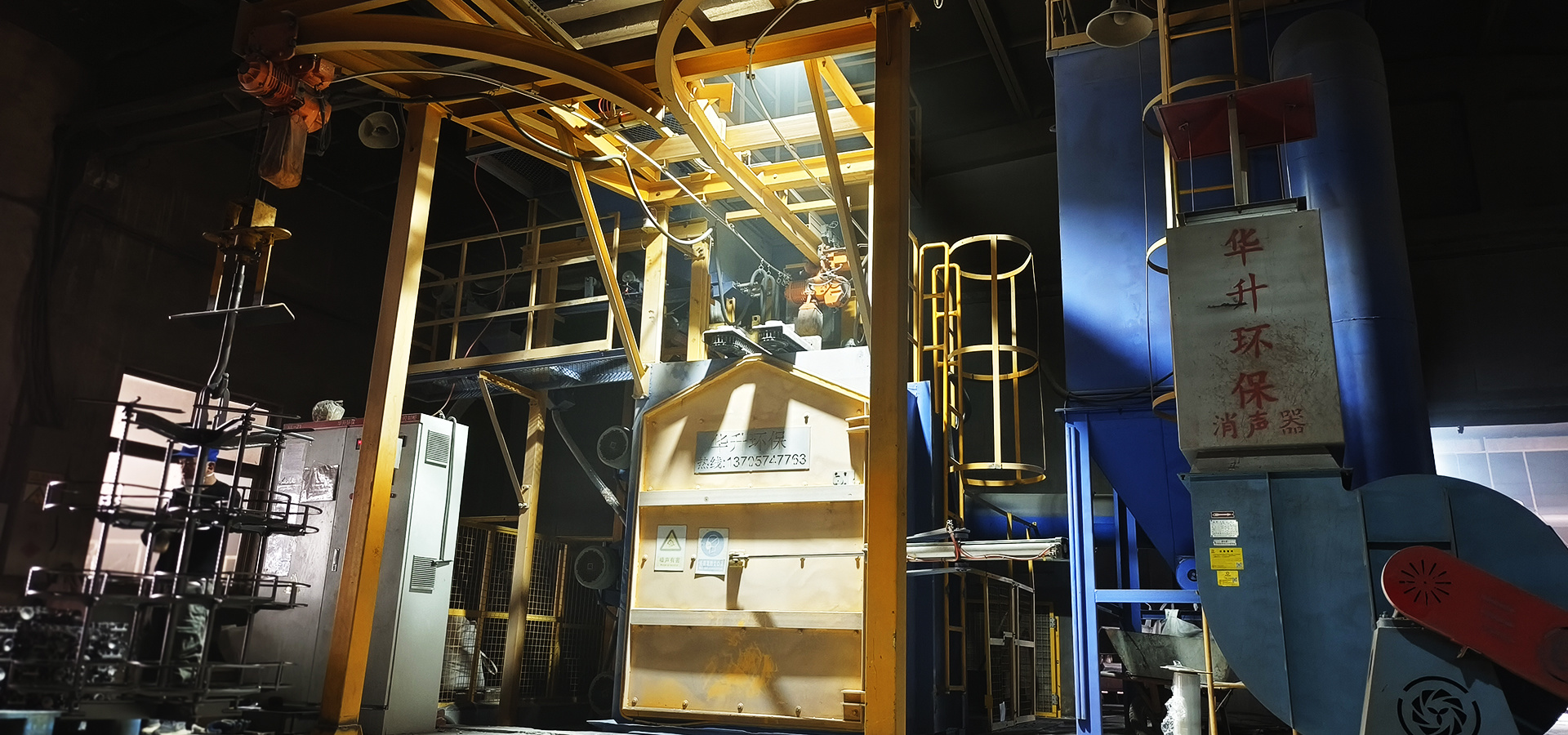
08
Shot Blasting & Clear
Shell removal using Φ0.5 mm cast steel shot at 0.4-0.6 MPa,It only takes 20 minutes to remove the casting shell
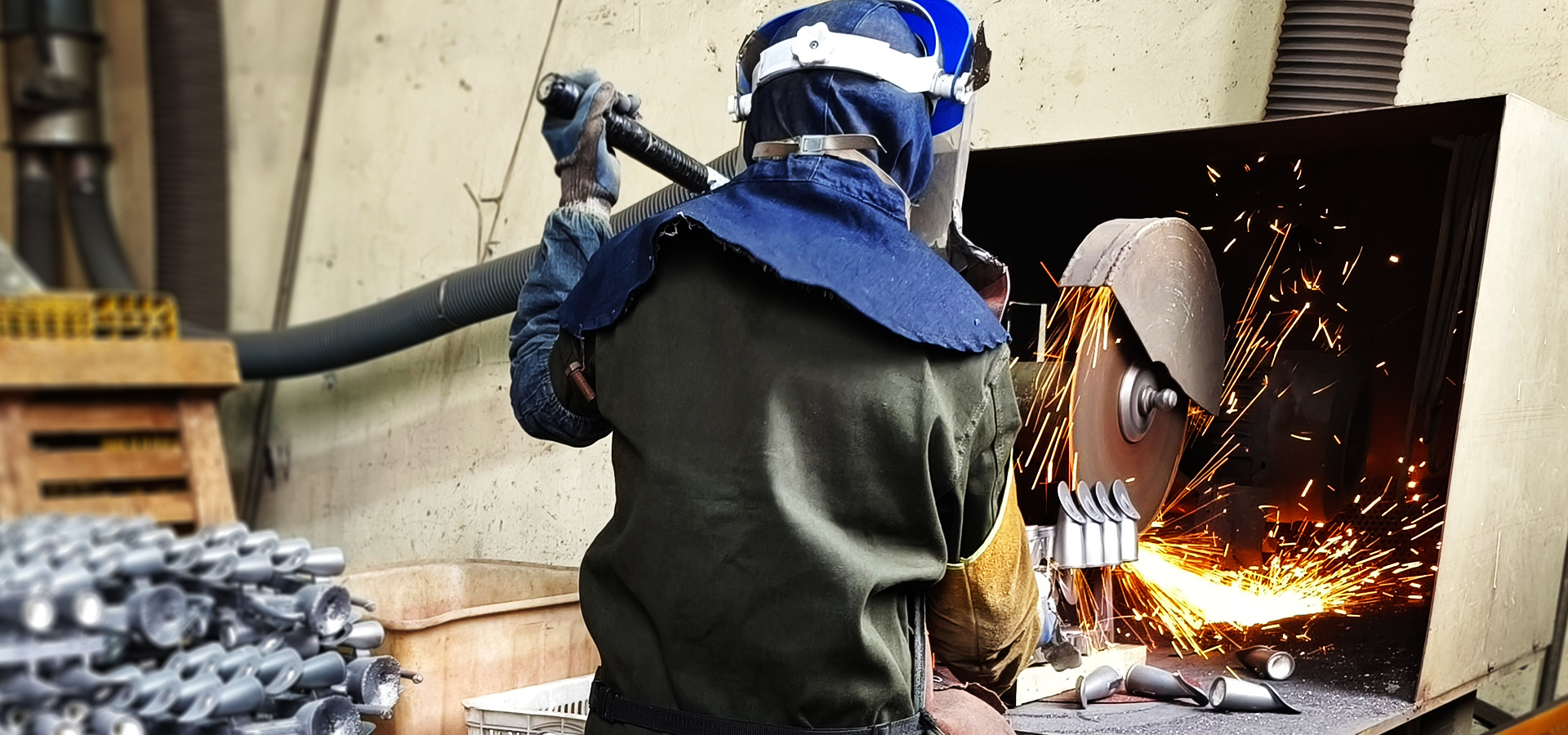
09
Cutting
Grinding wheel gate removal with ≤1.5 mm allowance, cutting temperature <200°C (to prevent microstructural degradation).
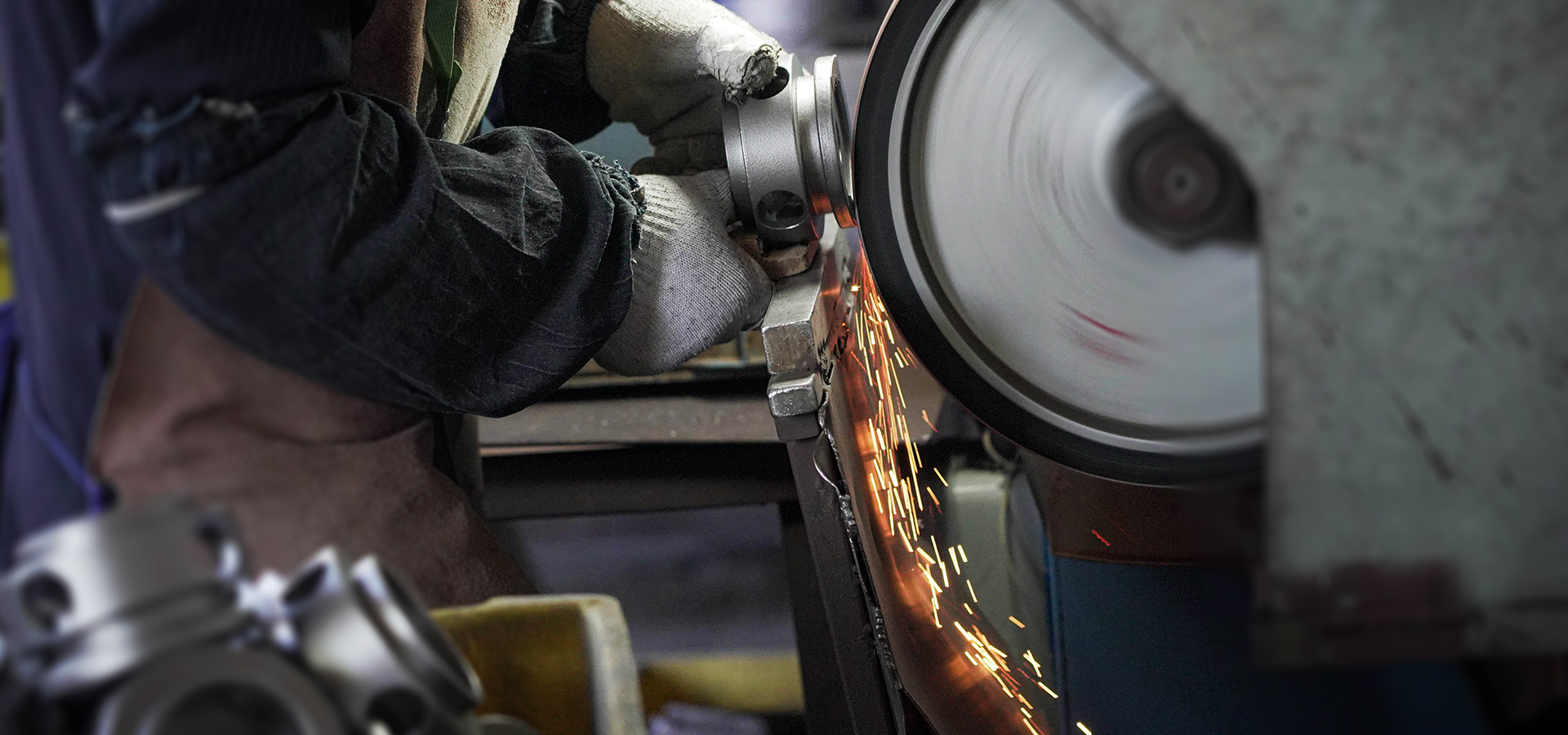
10
Gate Grinding
Resin-bonded grinding wheel (120 grit) for gate finishing, residual gate height ≤0.3 mm, transition radius R≥0.5 mm.
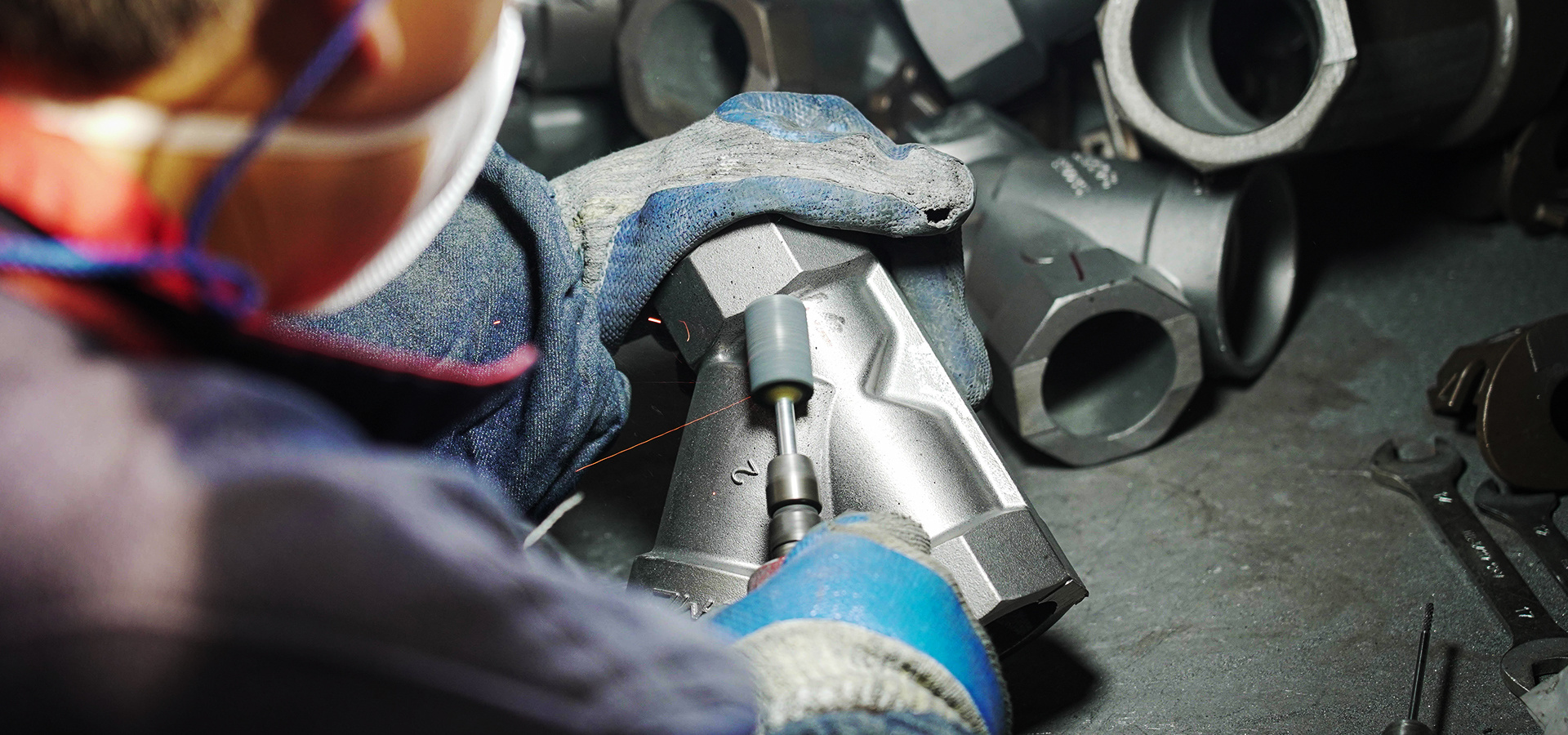
11
TIG Welding & Finishing
Argon shielding (purity ≥99.999%), ER316L filler wire, post-weld grinding to Ra ≤6.3 μm.
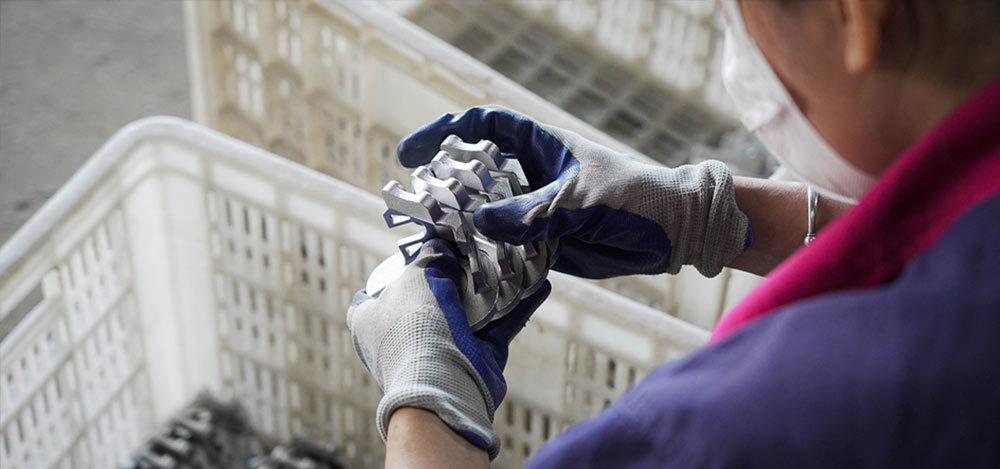
12
Final Inspection
PT (penetrant testing), RT (X-ray), full dimensional inspection (CT6-CT8 per ISO 8062), compliant with AMS 2175/ISO 4990.
Some of our product catalogs
Investment casting is a manufacturing process in which a liquid material is poured into a ceramic mold, which contains a hollow cavity of the desired shape, and then allowed to solidify. The solidified part is the casting, which is broken away from the ceramic mold to complete the process. The steps within the investment casting process are as follows:
Product brochure download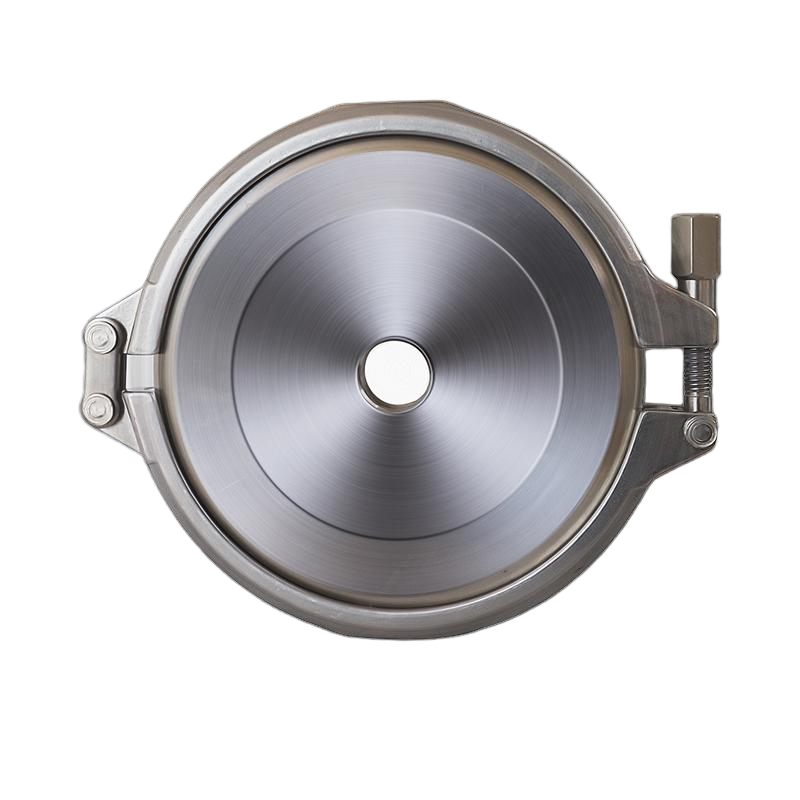
Clamp
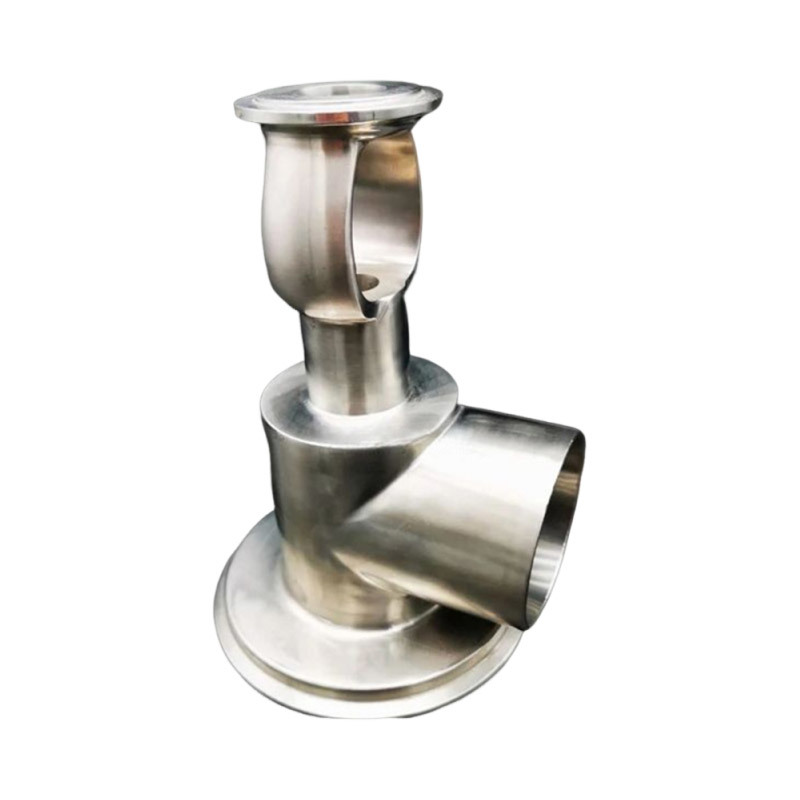
Chemical Liquid Precision Casting
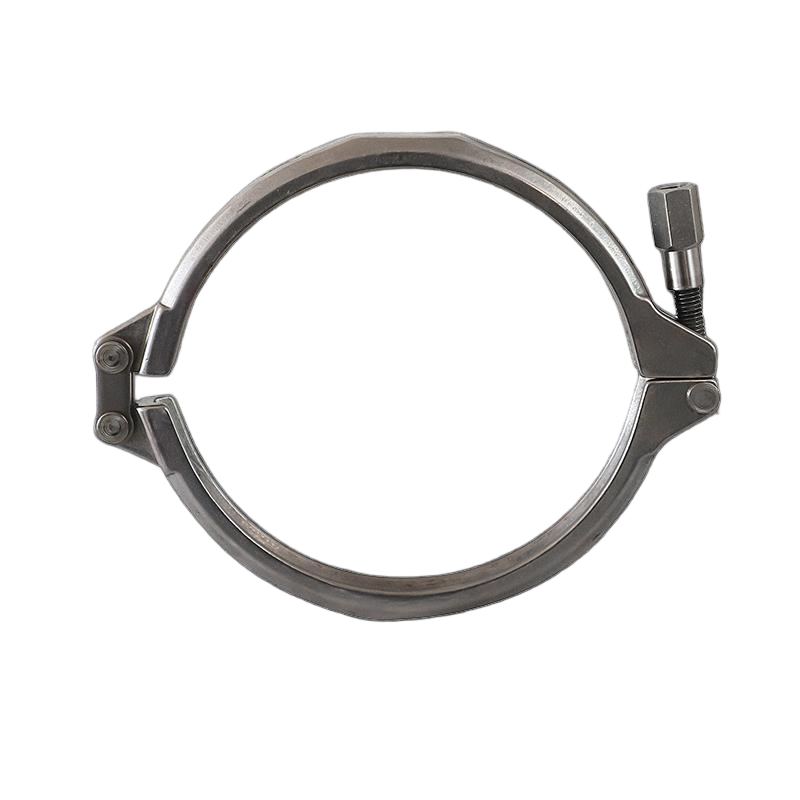
Clamp

Vane wheel
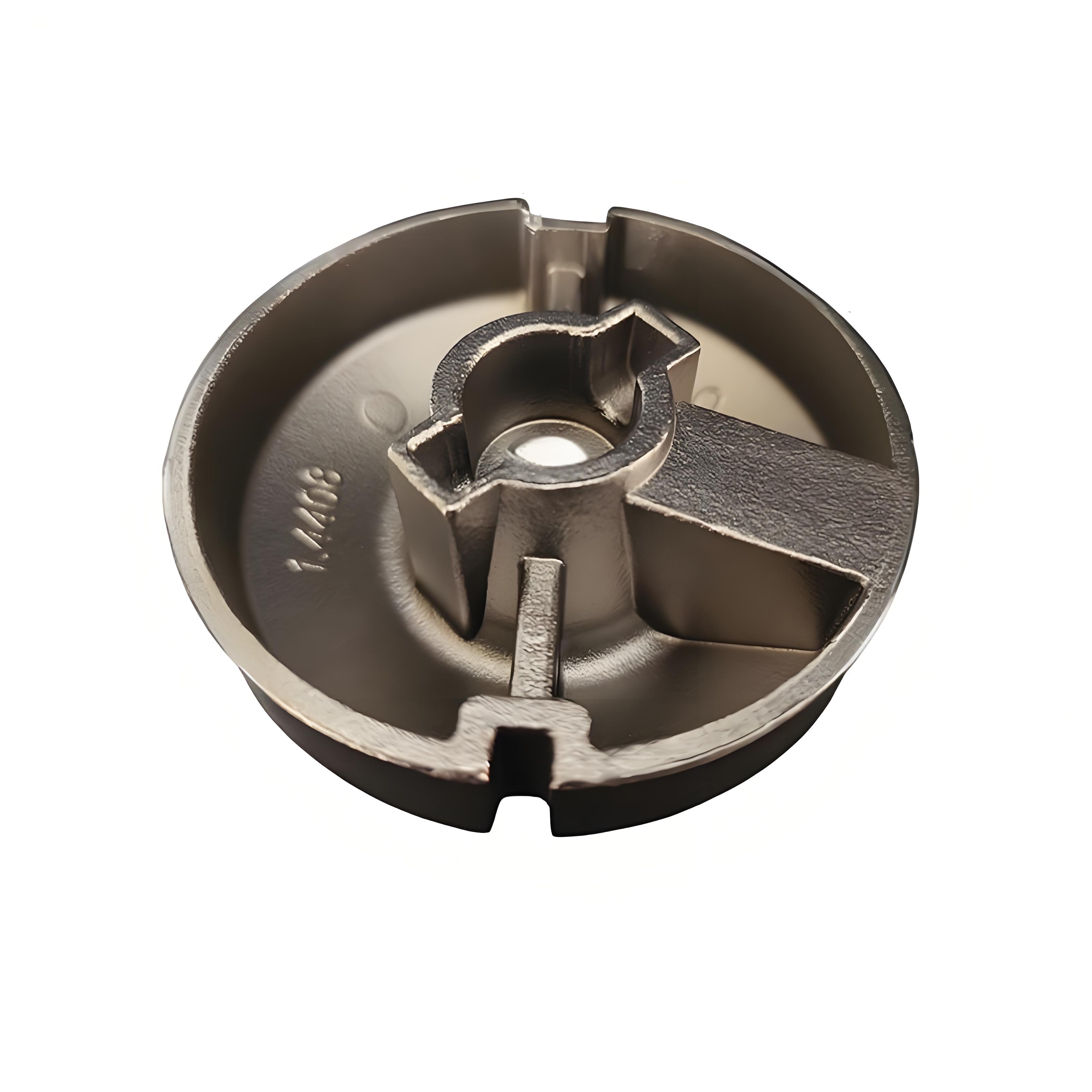
Chemical Liquid Precision Casting
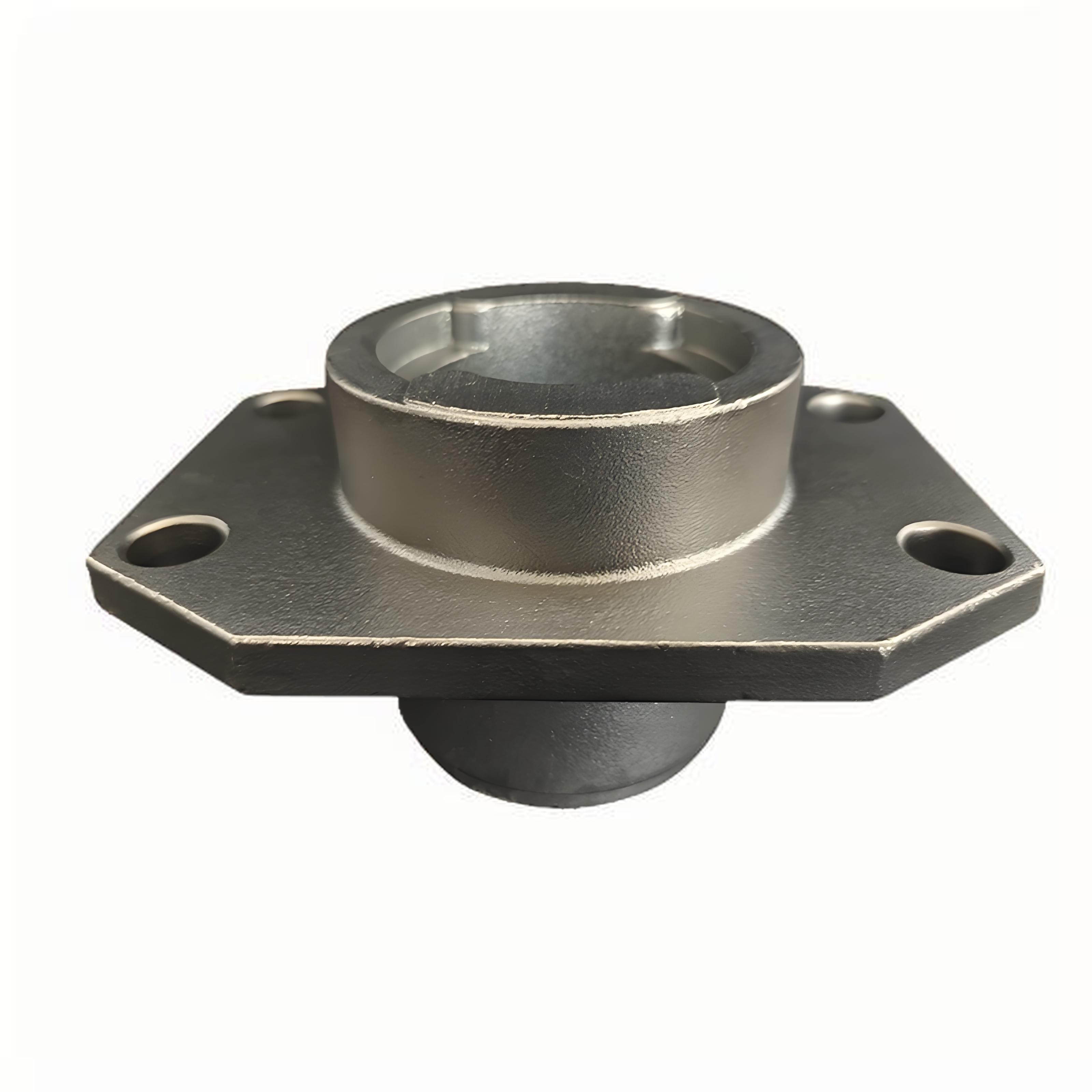
Chemical Liquid Precision Casting
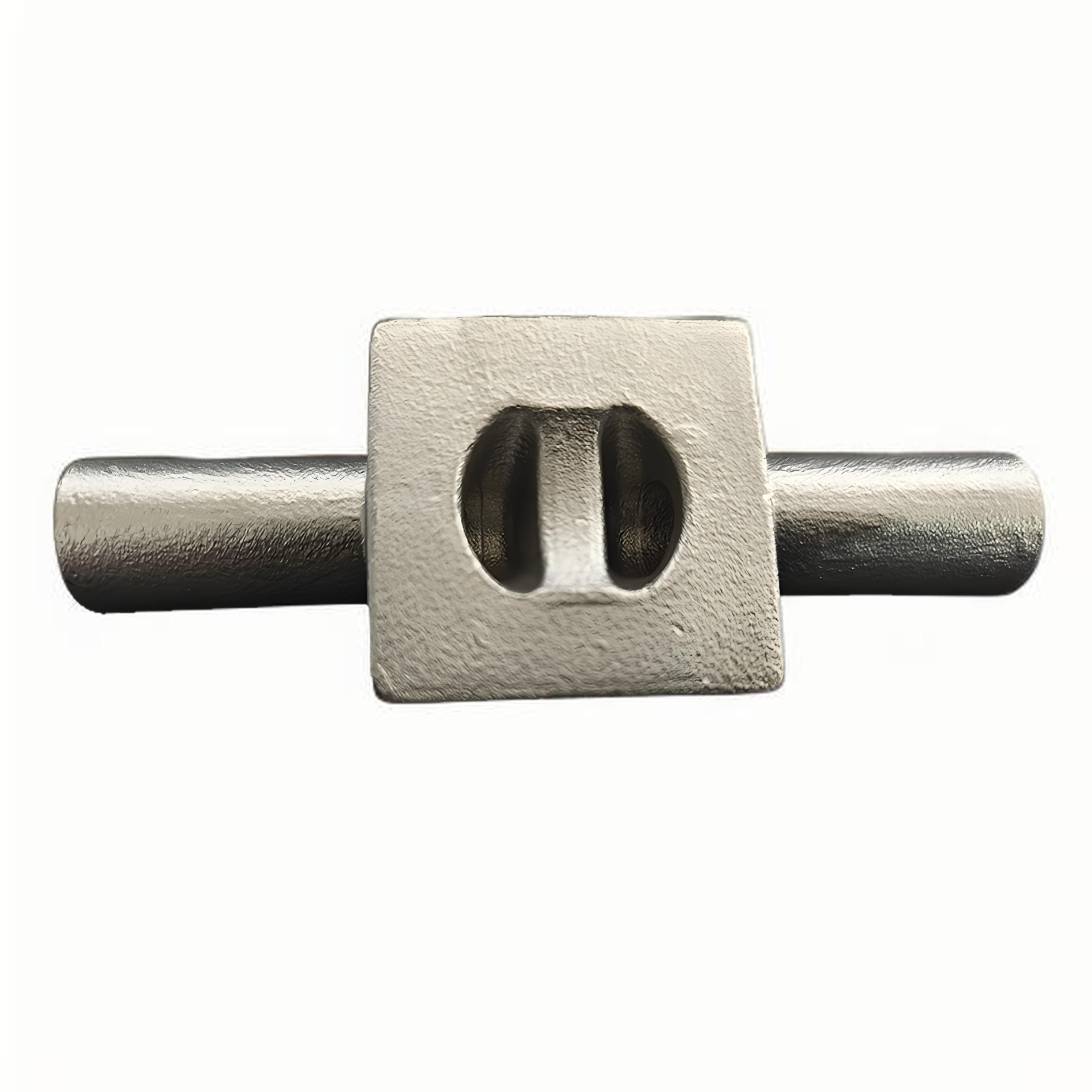
Chemical Liquid Precision Casting
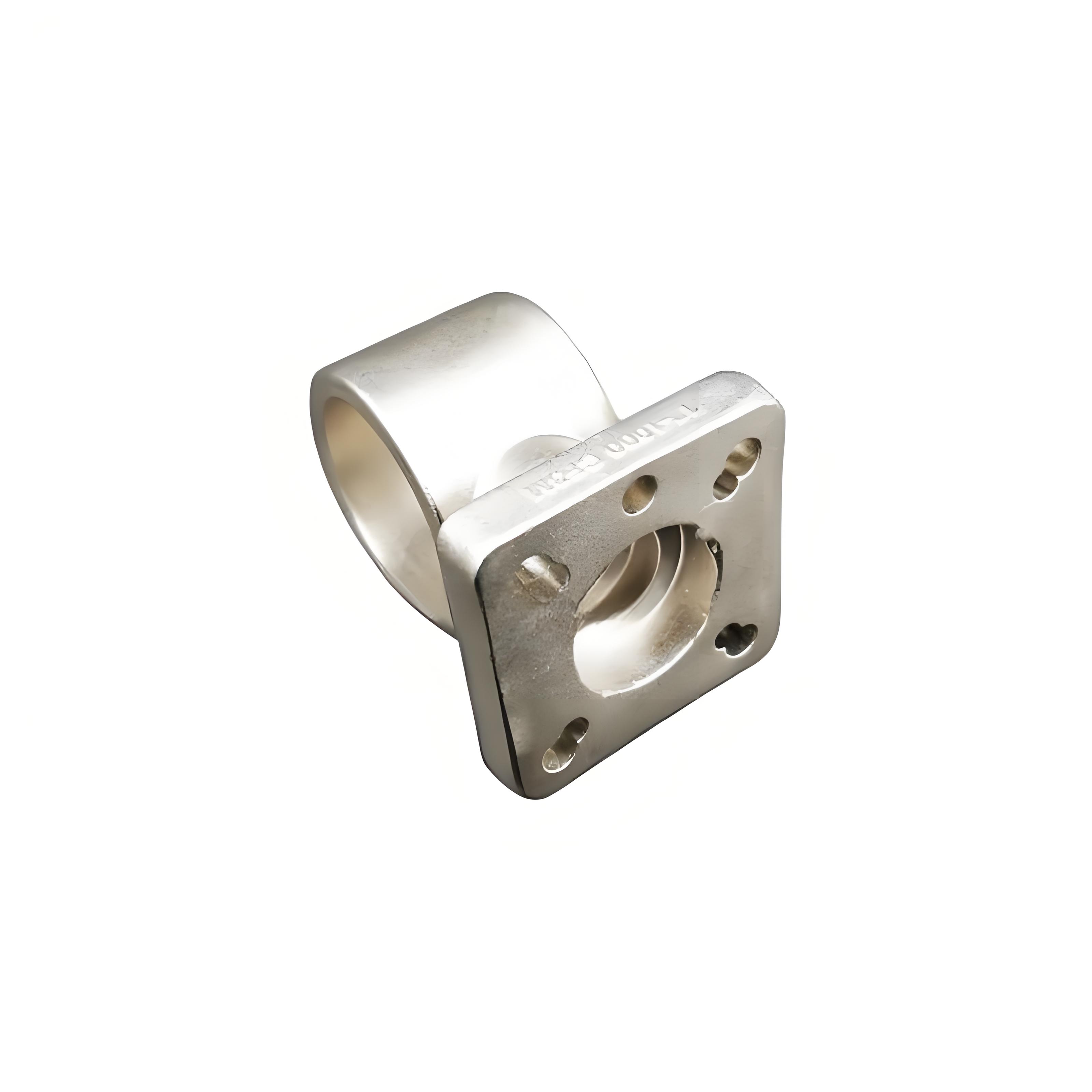
Chemical Liquid Precision Casting
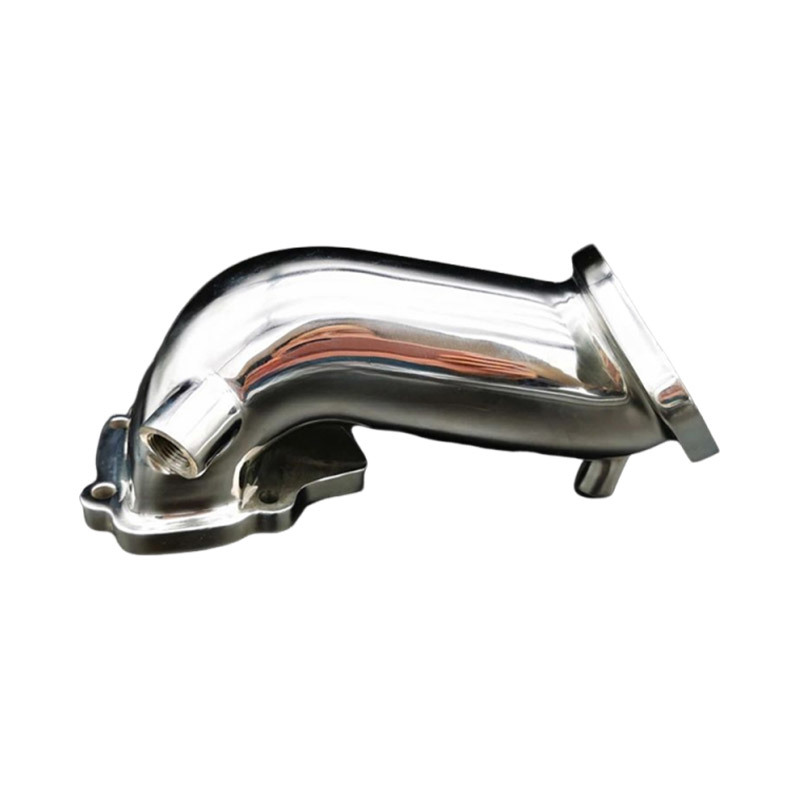
Chemical Liquid Precision Casting
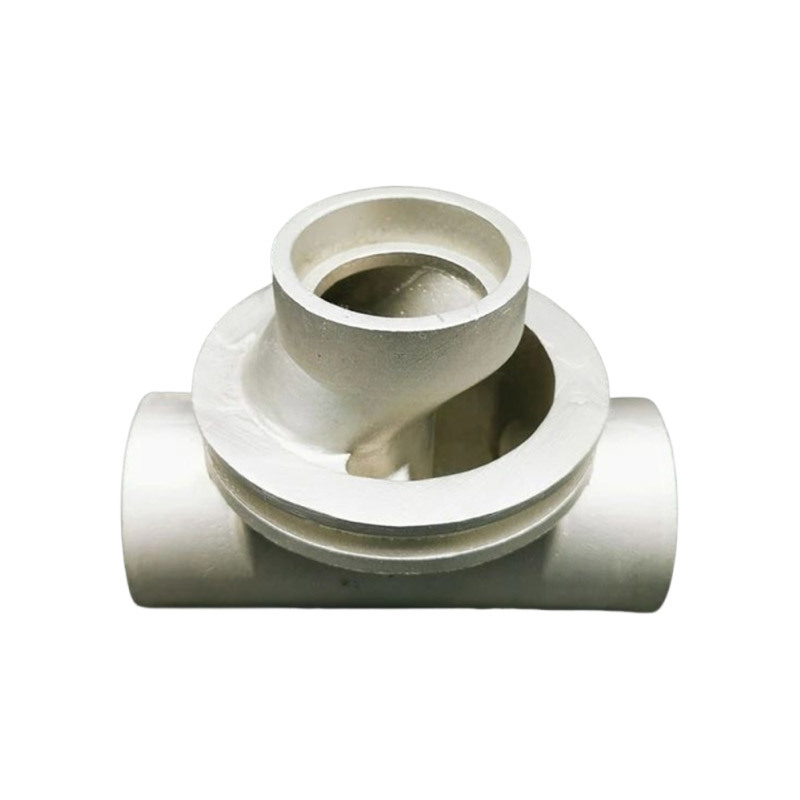
Chemical Liquid Precision Casting
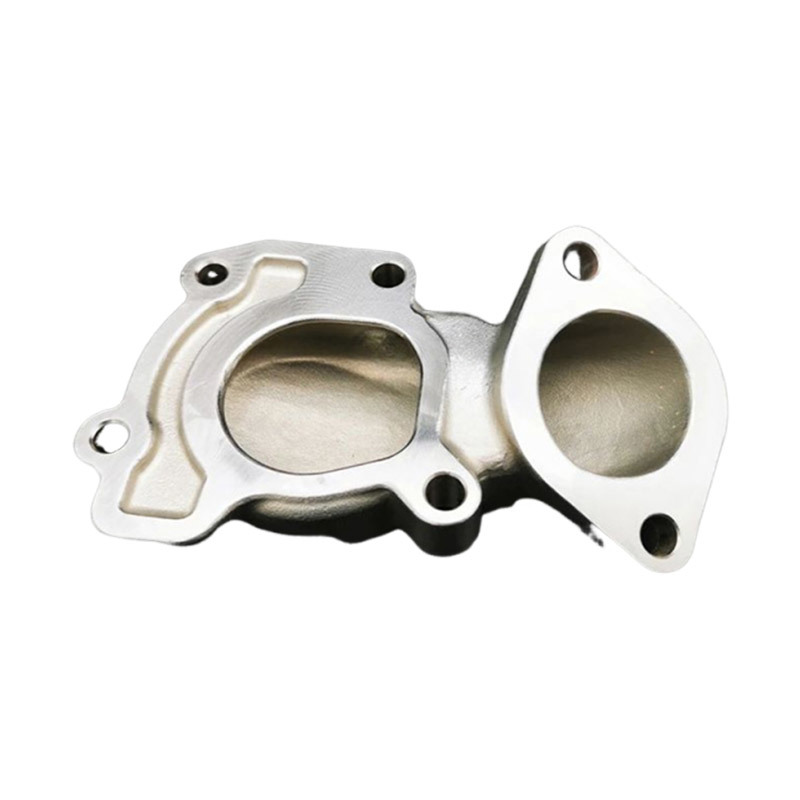
Chemical Liquid Precision Casting
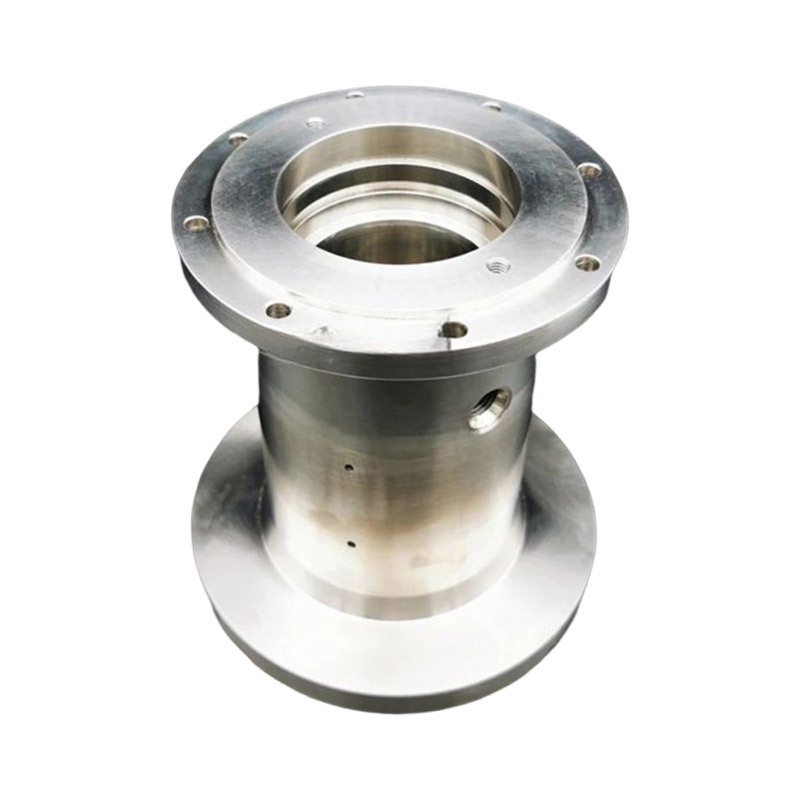
Chemical Liquid Precision Casting
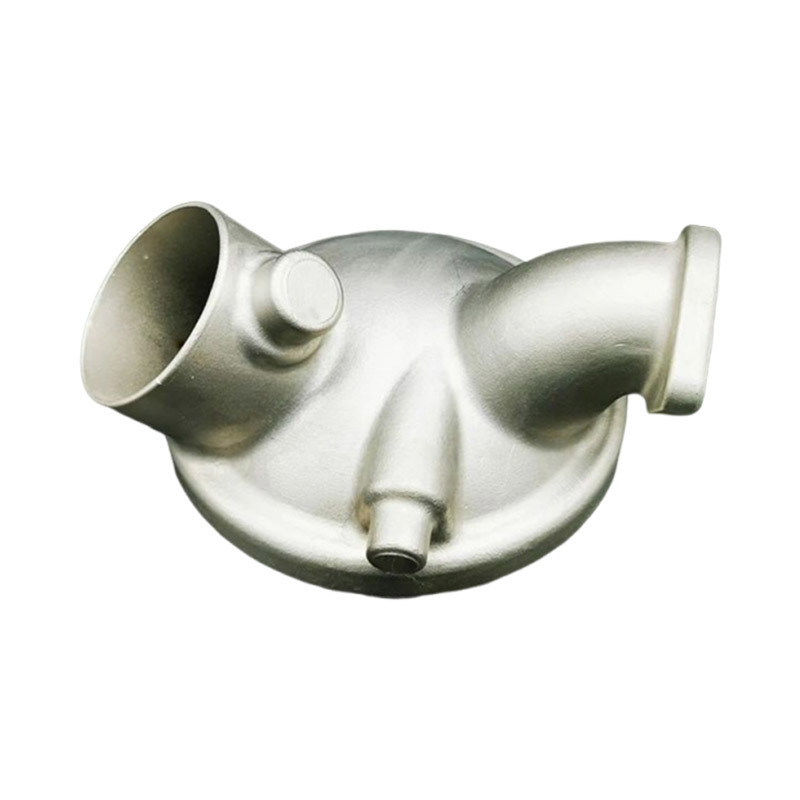
Chemical Liquid Precision Casting