
Application of precision casting in the field of pumps and valves
Ship precision casting refers to the technology of producing key components of ships through high-precision casting processes, which is widely used in fields such as navigation equipment, power systems, deck machinery, and marine engineering equipment. Its core goal is to achieve high strength, corrosion resistance, and reliability of components in complex marine environments (high salt spray, high corrosion, high load). With the development of the global shipbuilding industry, precision cast components are becoming increasingly popular and applied to various systems and equipment of ships.
Our achievements in the field of shipbuilding
We have been cooperating with multiple international shipping companies and traders since 1998, participating in the development and production of ship hardware, rope collectors, marine lifting equipment, turbines, valves, pipe fittings, impellers and other products.
Our capabilities in the field of pumps and valves
1. Due to the extremely strict requirements for materials and high corrosion resistance in the shipbuilding industry, it is necessary to resist seawater (including corrosive media such as Cl ⁻, SO ₄² ⁻) and marine atmospheric erosion. Therefore, the materials we commonly use include stainless steel (such as 316L, 904L, used for pump valves and piping components); Dual phase steel (components for offshore oil fields); Nickel based alloys (such as Inconel 625, resistant to seawater corrosion and high temperatures, used for turbine blades); Copper alloys (such as aluminum bronze and tin bronze, resistant to biological adhesion, used for propellers and bearings).
Parameter
Category |
Parameters |
Casting Materials |
Common materials: Carbon steel, stainless steel, alloy |
Material weight range: 0.003 kg - 110 kg |
|
Casting Dimensions |
Maximum casting size: Ø600mmX800mm |
Minimum casting size: 5 mm x 5 mm x 5 mm |
|
Casting wall thickness: 1 mm - 20 mm |
|
Casting Precision |
Dimensional tolerance: ±0.05 mm - ±0.2 mm (depending on casting size) |
Surface roughness: Ra 3.2 µm -6.3 µm |
|
Production Capacity |
Annual output: 600 tons |
Maximum single piece weight: 110 kg |
|
Minimum single piece weight: 3 grams |
|
Mold materials: Wax molds, ceramic molds |
|
Casting Process |
Mold types: Precision wax mold casting |
Pouring methods: Gravity casting, vacuum casting |
|
Heat Treatment Capability |
Heat treatment processes: Normalizing, annealing, quenching, tempering |
Treatment furnace temperature range: 600℃ - 1100℃ |
|
Post-Processing |
Surface treatment: Polishing, sandblasting, machining, painting, hot-dip galvanizing, powder coating |
We strictly control the quality of our products. Key components undergo the following tests:
1. Non destructive testing: ultrasonic testing (UT) to detect internal defects, and magnetic particle testing (MT) to screen for surface cracks;
2. Mechanical performance tests: tensile test, impact test (-20 ℃ low-temperature impact energy ≥ 27J), fatigue test (simulating 10 ⁶ load cycles);
3. Environmental simulation testing: salt spray test (500 hours without corrosion), high-pressure water tightness test (if the valve housing can withstand a pressure of 10MPa without leakage).
4. Our precision casting technology parameters: dimensional tolerance can reach ± 0.1mm, surface roughness Ra ≤ 6.3 μ m, suitable for complex small parts. Ceramic shell multi-layer coating (such as zirconia+alumina, resistant to high temperatures above 1600 ℃). Turbocharger blades, nickel based alloy, blade thickness 0.8-1.5mm; precision valve components such as pressure reducing valve cores require a clearance of ≤ 0.03mm.
Instant inquiry
Products in the pump and valve field are mostly shaped parts, and have high sealing and pressure resistance requirements, so they are more suitable for stainless steel precision casting technology.
Technological Process
Investment casting is a manufacturing process in which a liquid material is poured into a ceramic mold, which contains a hollow cavity of the desired shape, and then allowed to solidify. The solidified part is the casting, which is broken away from the ceramic mold to complete the process. The steps within the investment casting process are as follows:
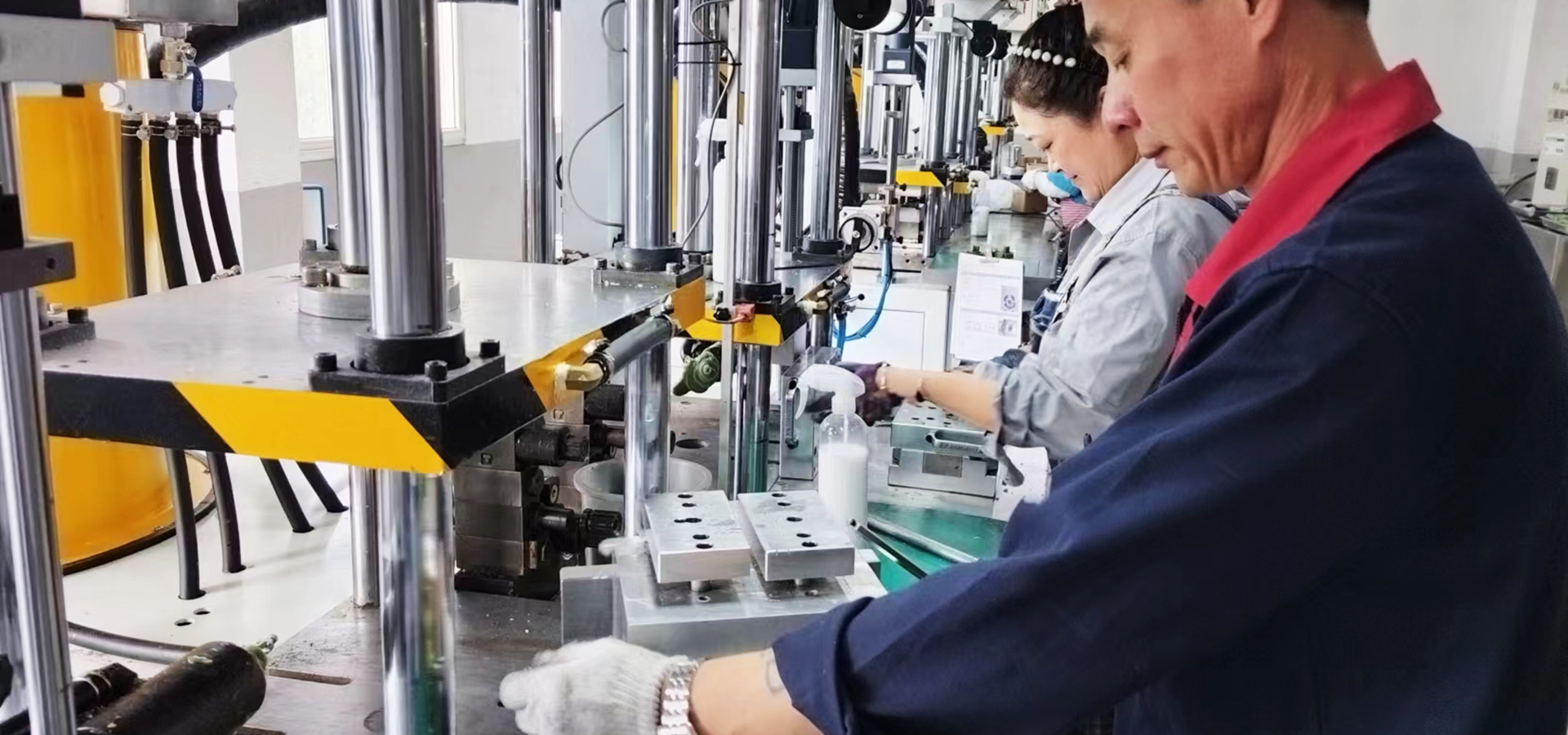
01
Wax Injection
Injection of medium-temperature wax (60-65°C) into metal molds under 0.5-0.7 MPa pressure, with a dwell time of 20-30 seconds.
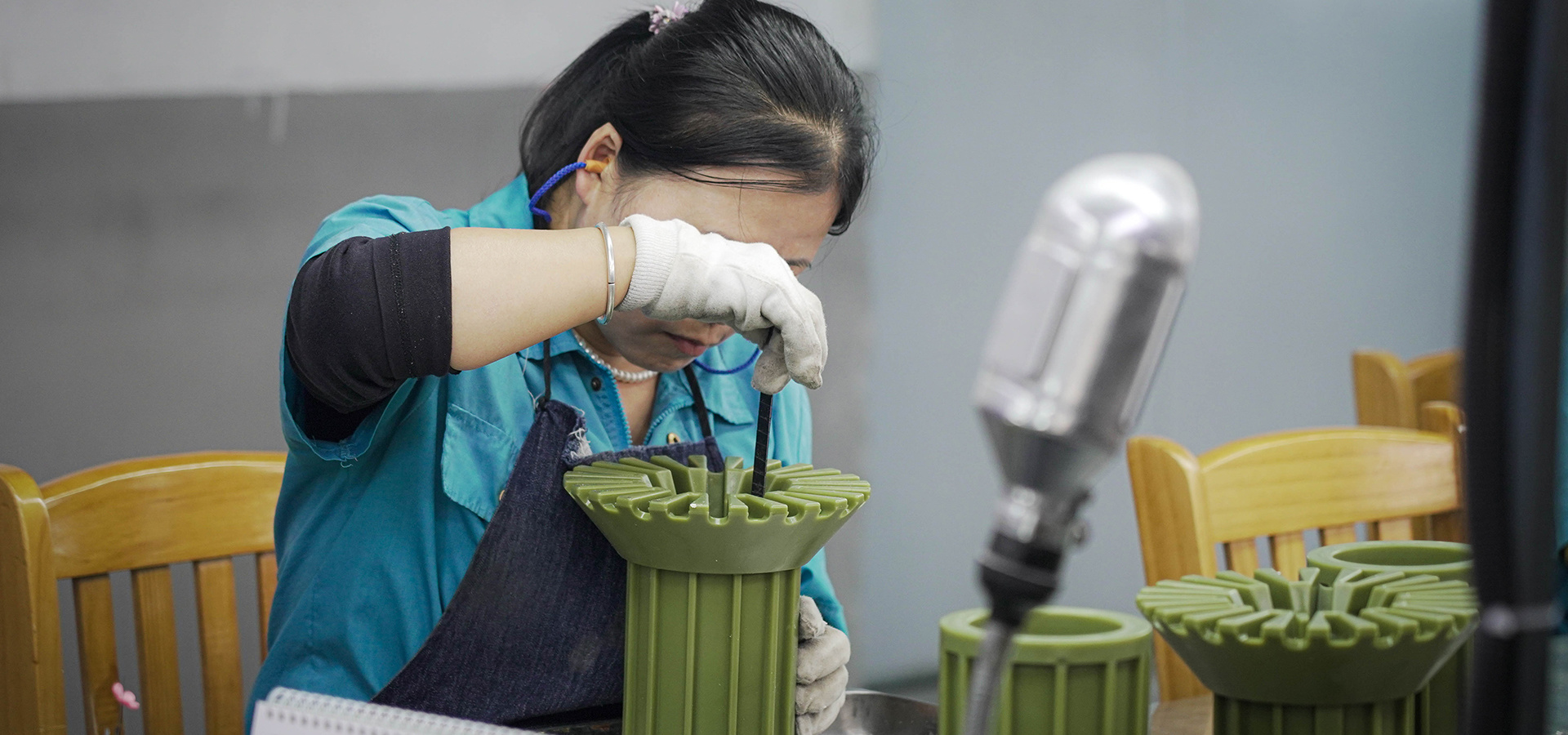
02
Wax Pattern Trimming
Removal of flash from wax pattern parting lines with precision ±0.1 mm, using hot knives (70-90°C)
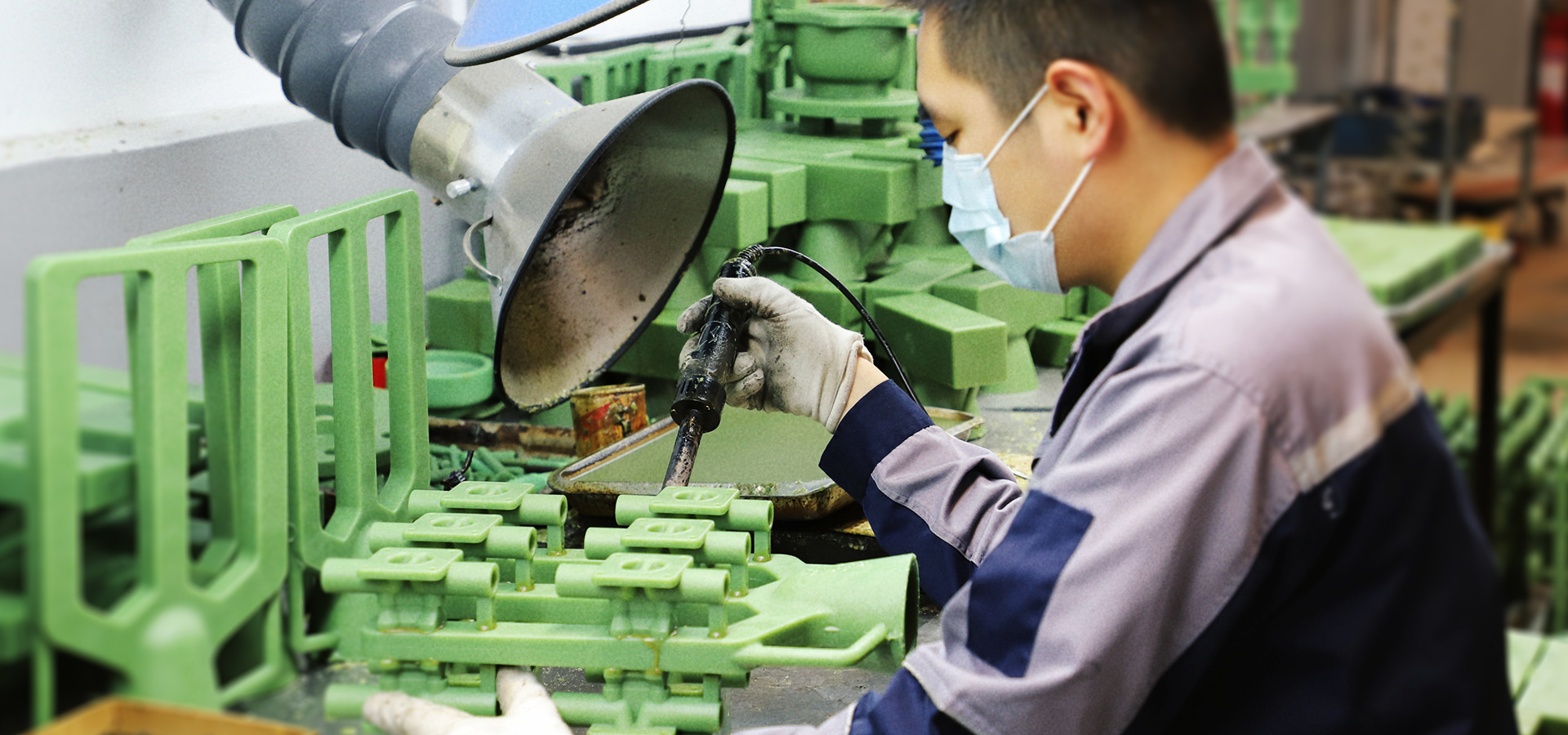
03
Cluster Assembly
Welding wax patterns to a central sprue, with cluster weight ≤15 kg, pattern spacing ≥8 mm, and pouring angle of 25-30°.
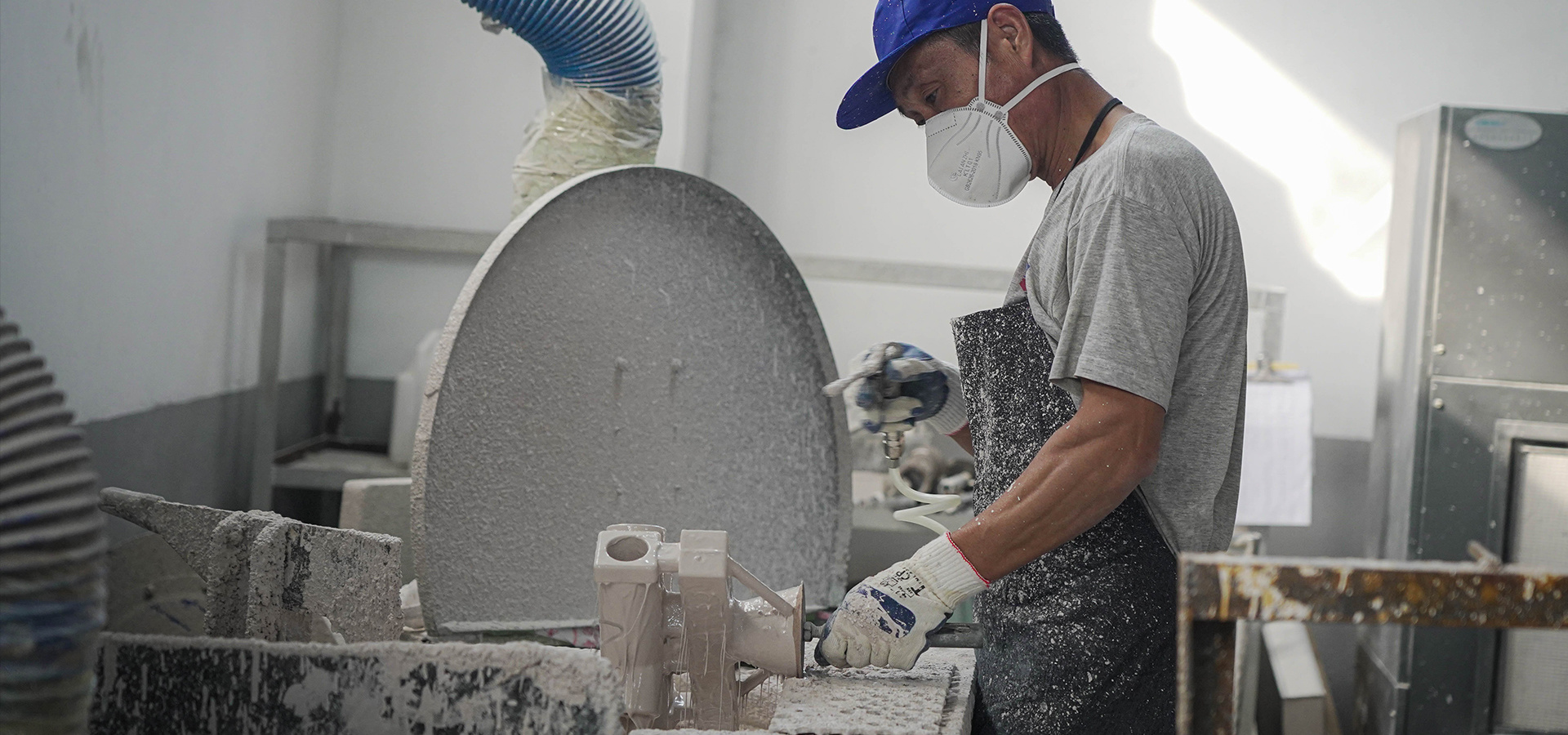
04
Primary Coating
Silica sol (SiO₂ 20%) + zircon flour (ZrO₂ 80%), 320-mesh,viscosity 42-45 seconds (#4 Zahn cup), coating thickness 0.3-0.5 mm.
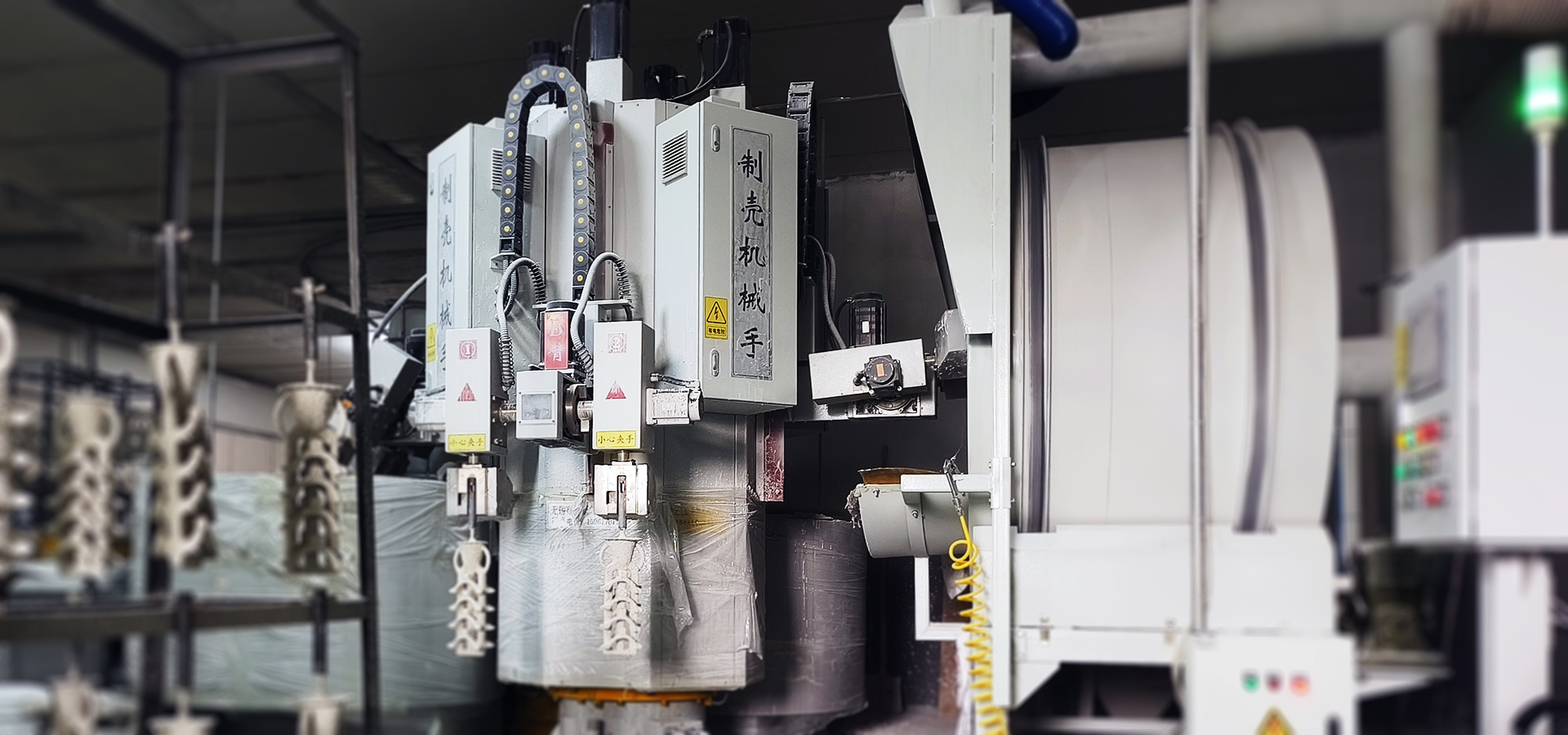
05
Backup
Quartz sand, 80~120-mesh 、30~60-mesh 、16~30-mesh chamotte sand stuccoing, total shell thickness 6-8 mm, green strength ≥4 MPa.
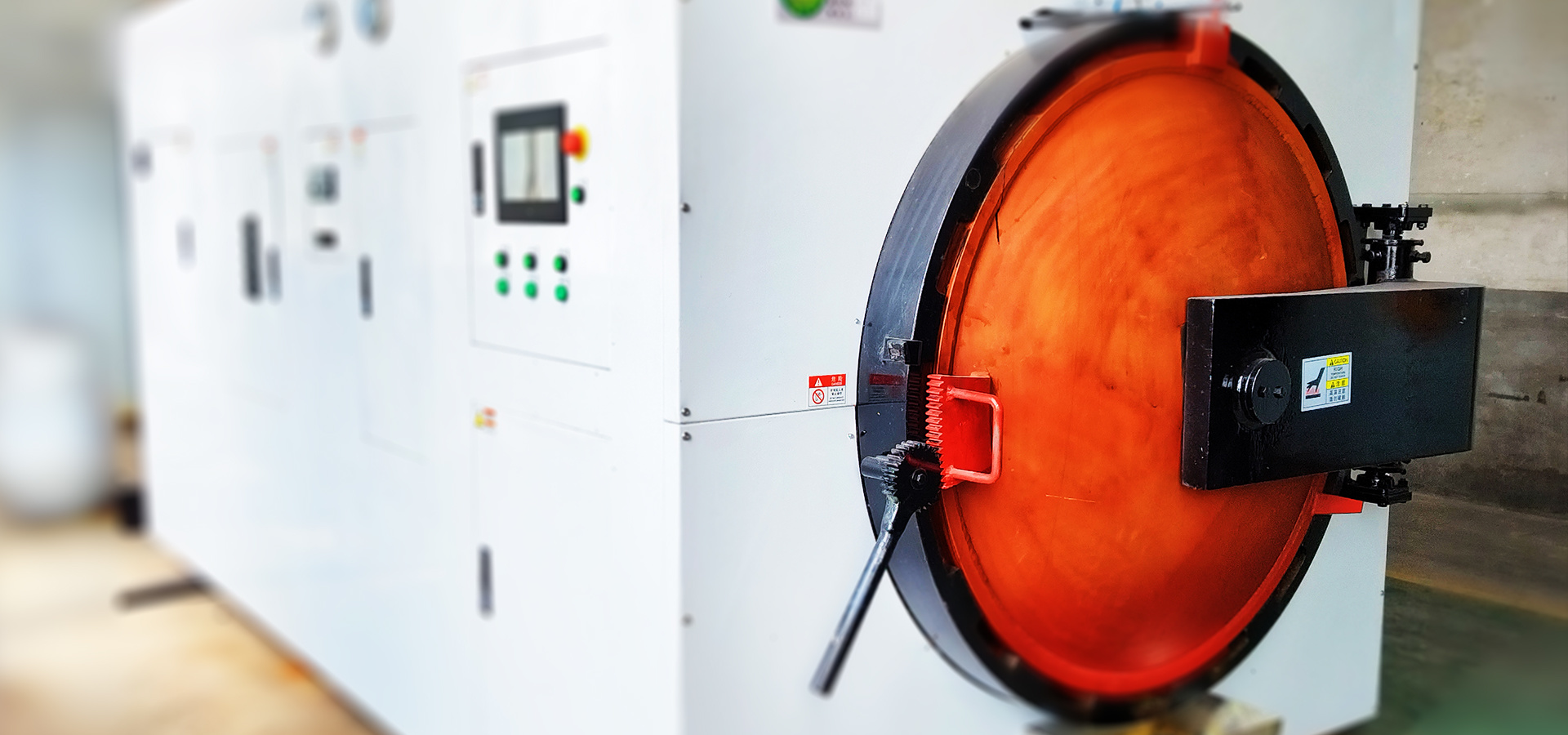
06
Dewaxing
High-pressure steam dewaxing (0.6-0.8 MPa, 150-170°C), residual wax ≤0.3%, shell breakage rate <0.5%.
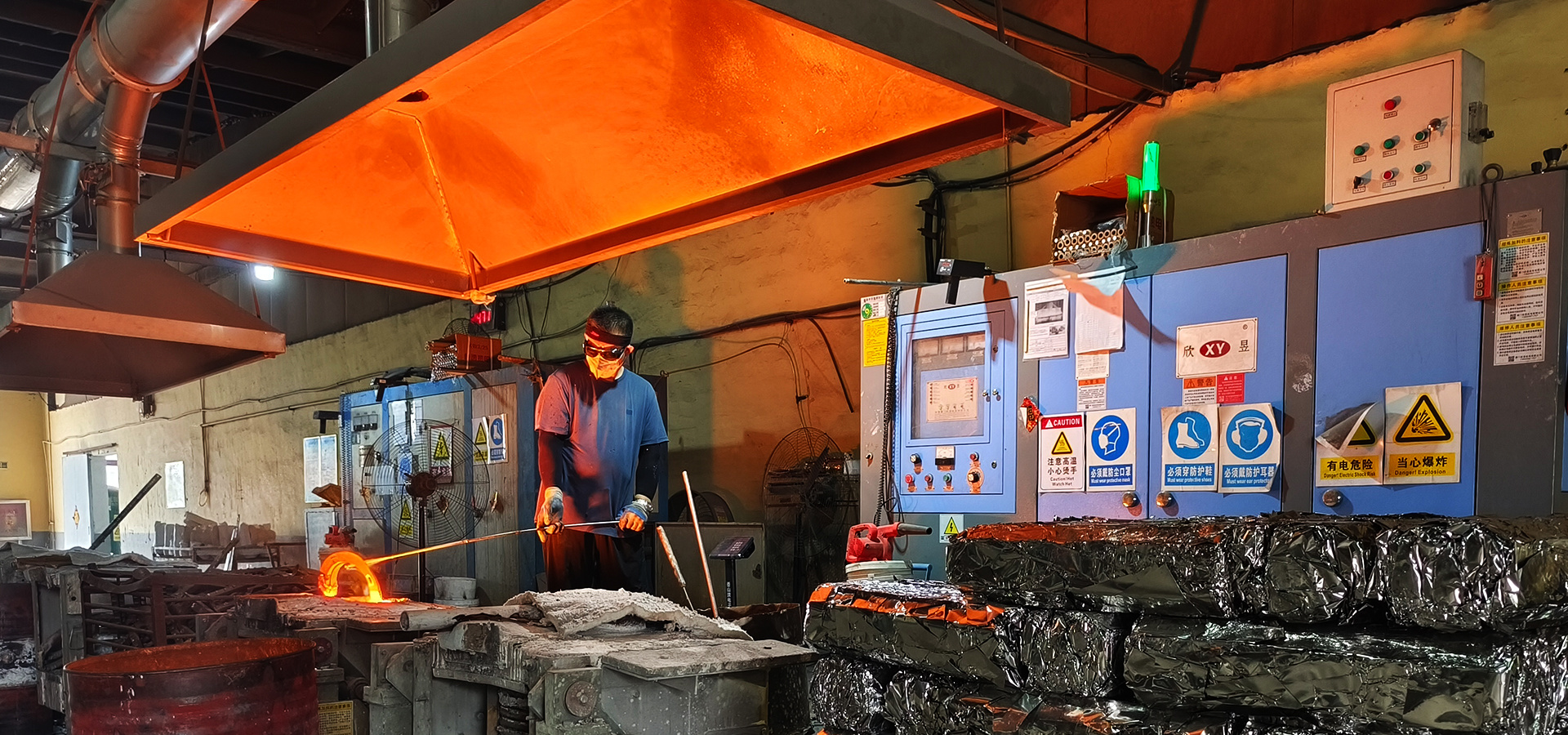
07
Pouring
Gravity casting with preheated molds (1000-1200°C), pouring rate 0.8-1.2 kg/s, solidification cooling rate 50-100°C/min.
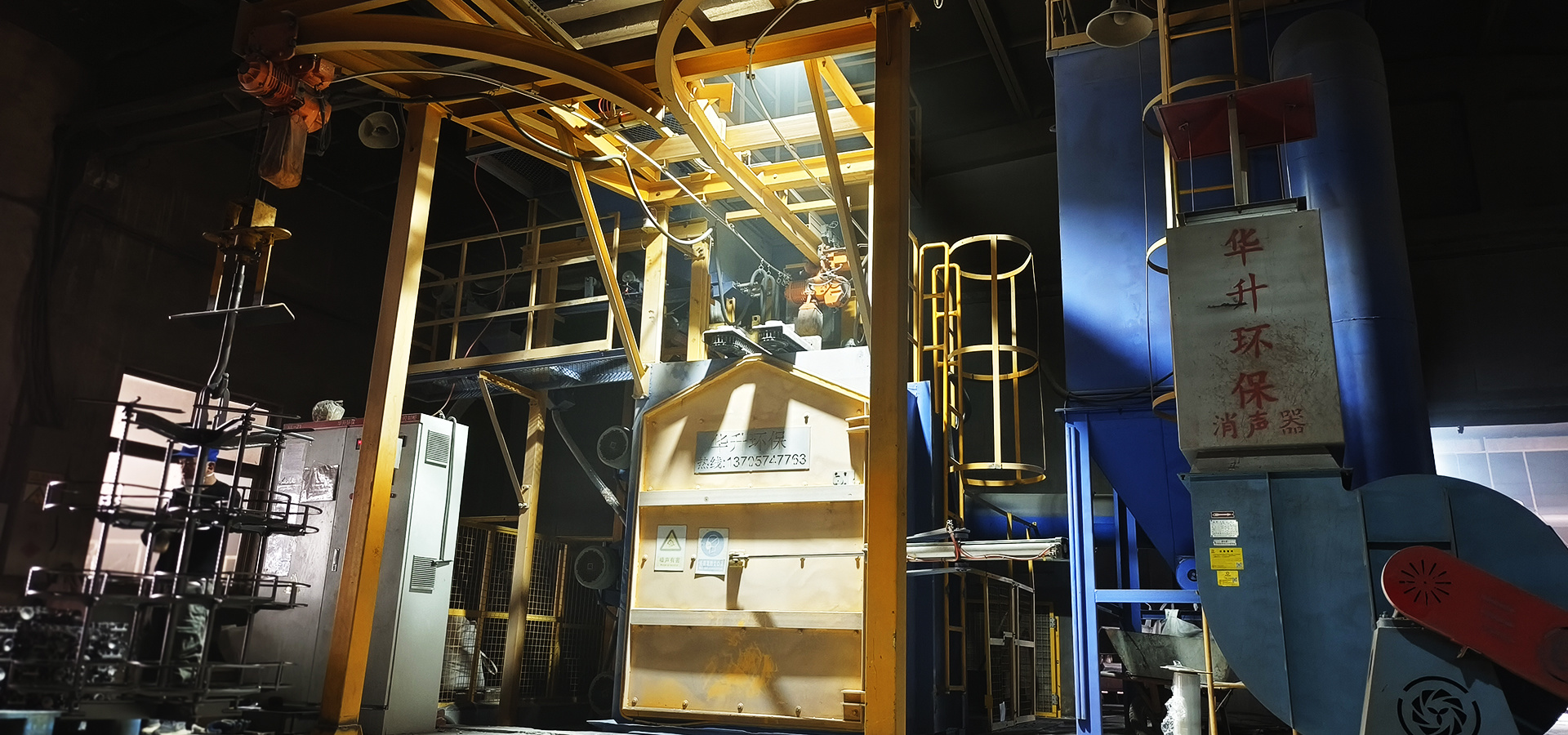
08
Shot Blasting & Clear
Shell removal using Φ0.5 mm cast steel shot at 0.4-0.6 MPa,It only takes 20 minutes to remove the casting shell
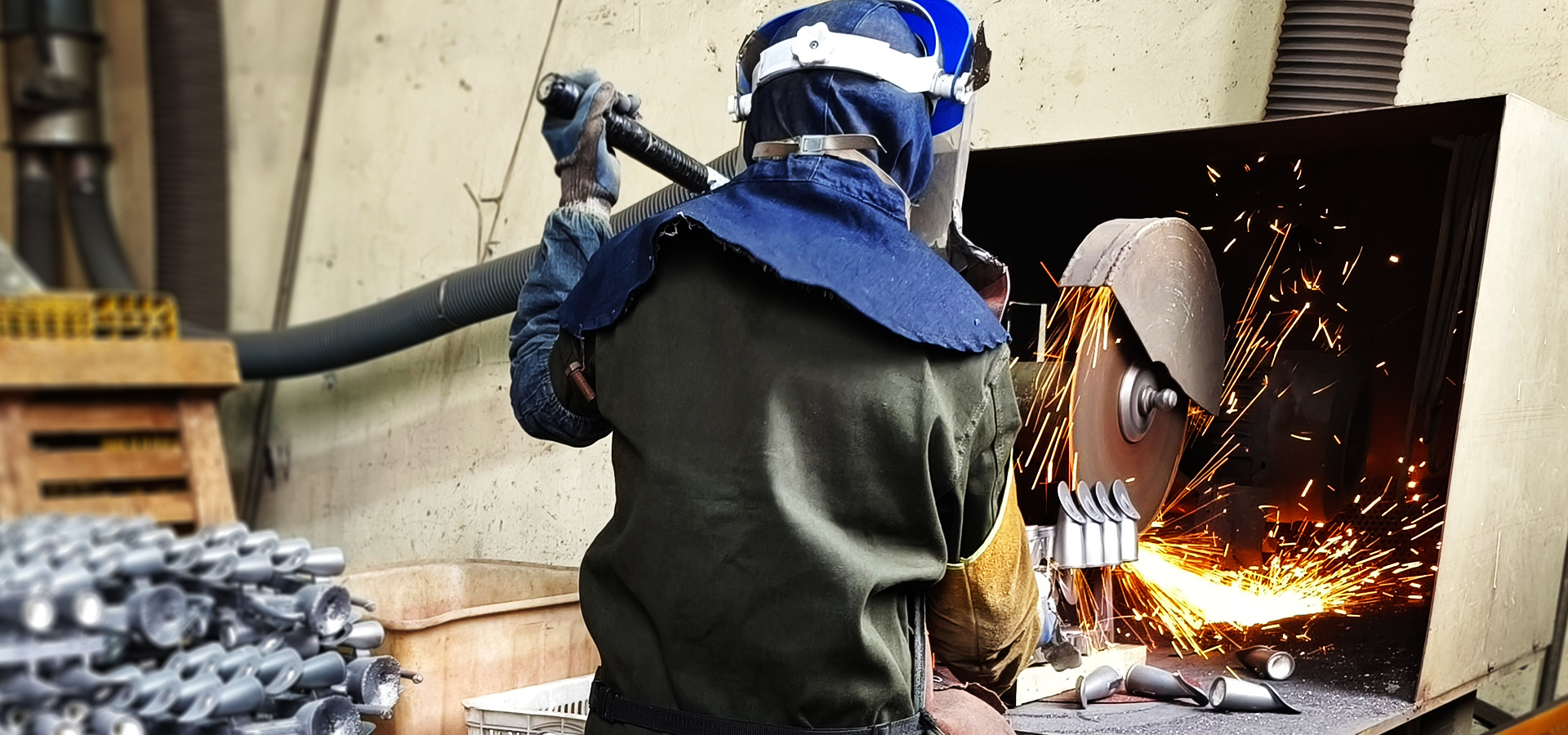
09
Cutting
Grinding wheel gate removal with ≤1.5 mm allowance, cutting temperature <200°C (to prevent microstructural degradation).
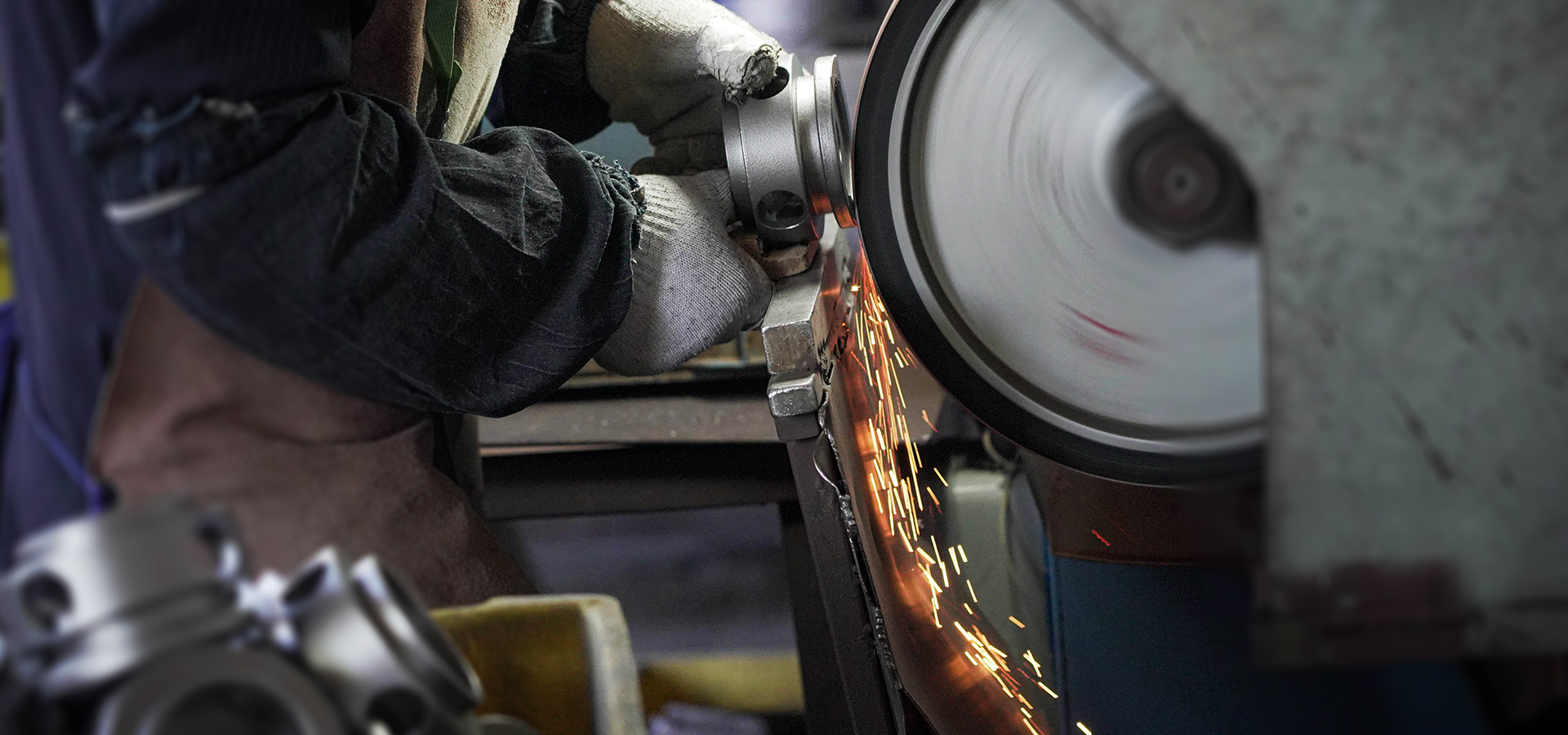
10
Gate Grinding
Resin-bonded grinding wheel (120 grit) for gate finishing, residual gate height ≤0.3 mm, transition radius R≥0.5 mm.
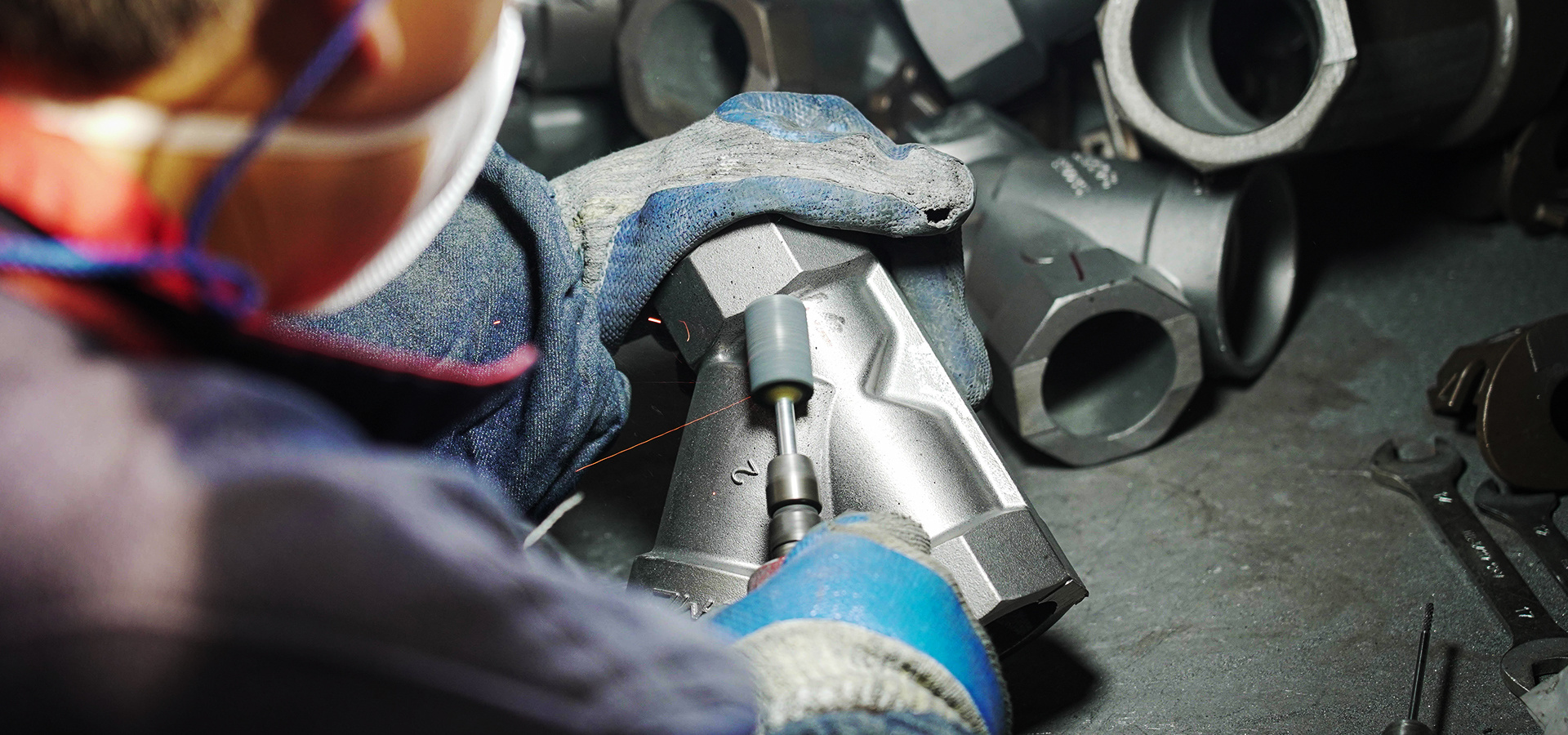
11
TIG Welding & Finishing
Argon shielding (purity ≥99.999%), ER316L filler wire, post-weld grinding to Ra ≤6.3 μm.
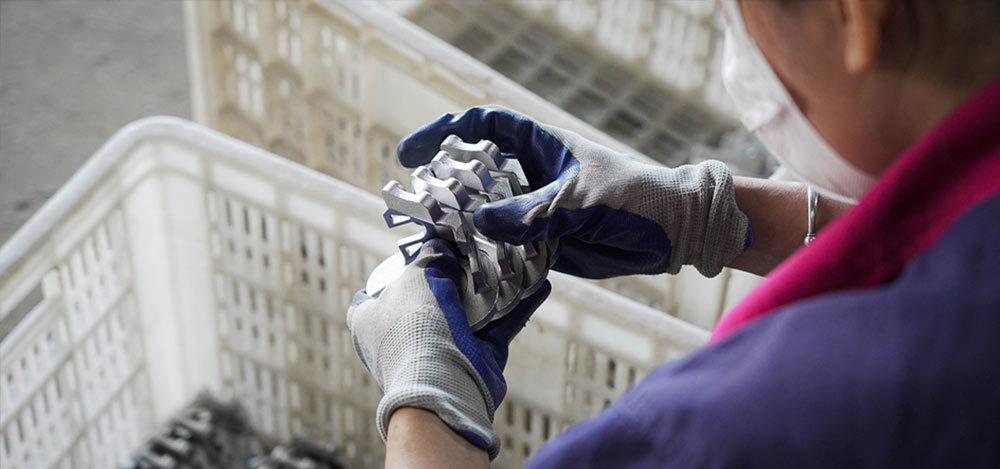
12
Final Inspection
PT (penetrant testing), RT (X-ray), full dimensional inspection (CT6-CT8 per ISO 8062), compliant with AMS 2175/ISO 4990.
Some of our product catalogs
Investment casting is a manufacturing process in which a liquid material is poured into a ceramic mold, which contains a hollow cavity of the desired shape, and then allowed to solidify. The solidified part is the casting, which is broken away from the ceramic mold to complete the process. The steps within the investment casting process are as follows:
Product brochure download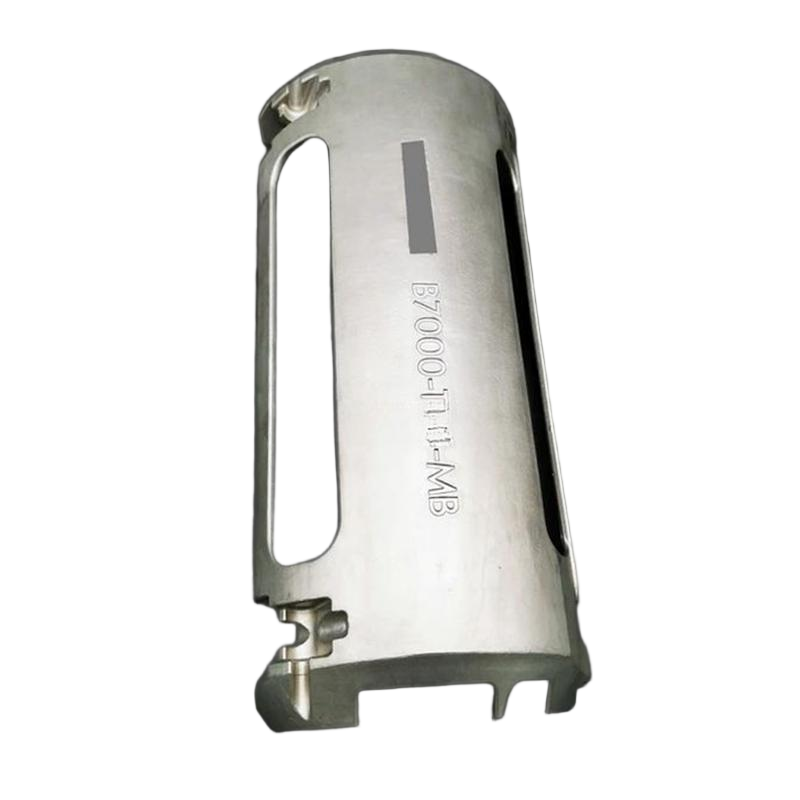
Precision casting in the field of ship safety
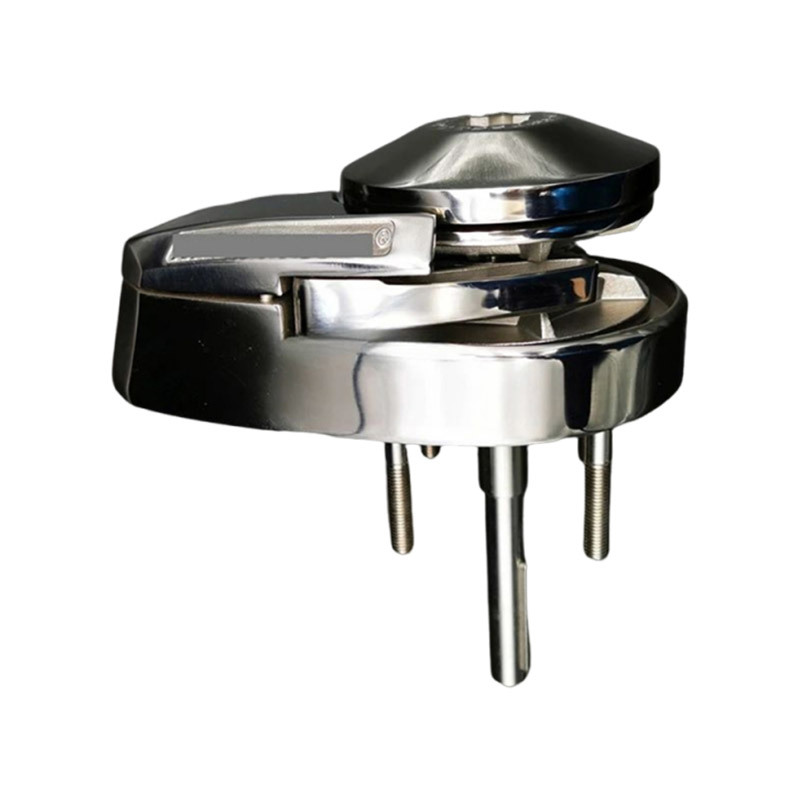
Precision casting in the field of ship safety
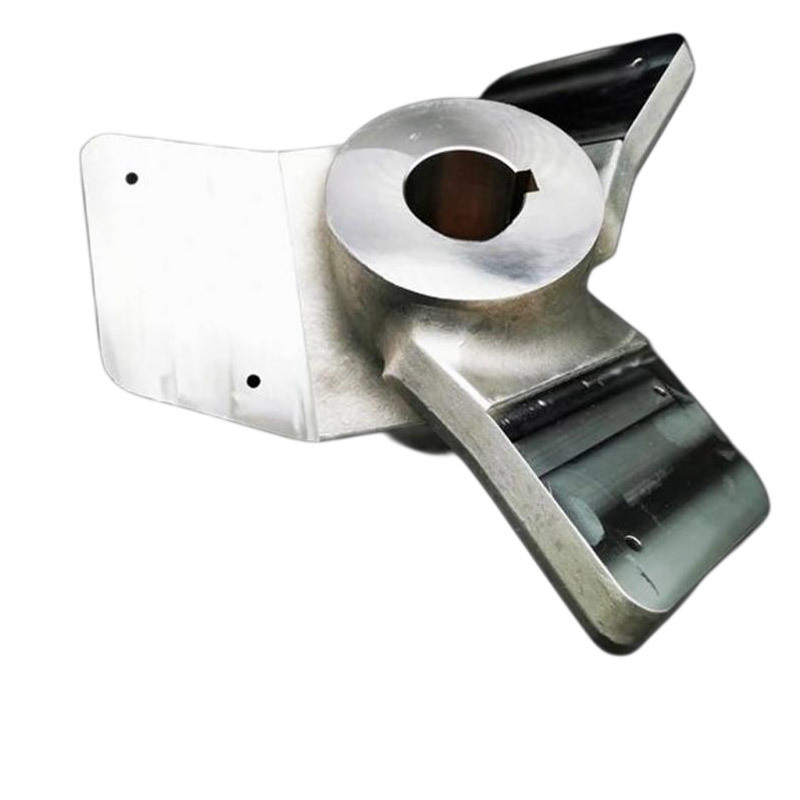
Precision casting in the field of ship safety
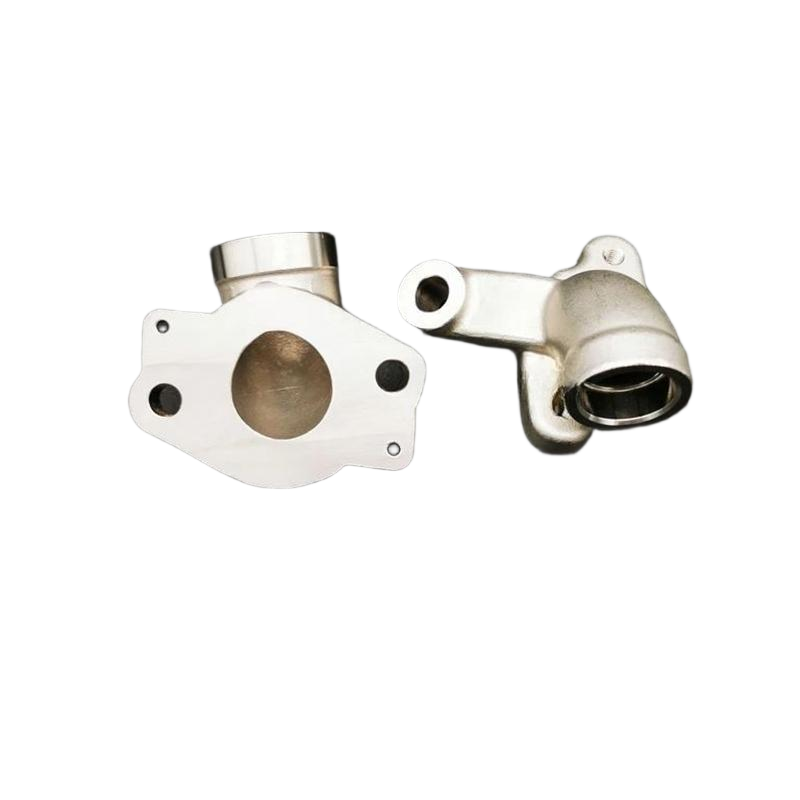
Precision casting in the field of ship safety
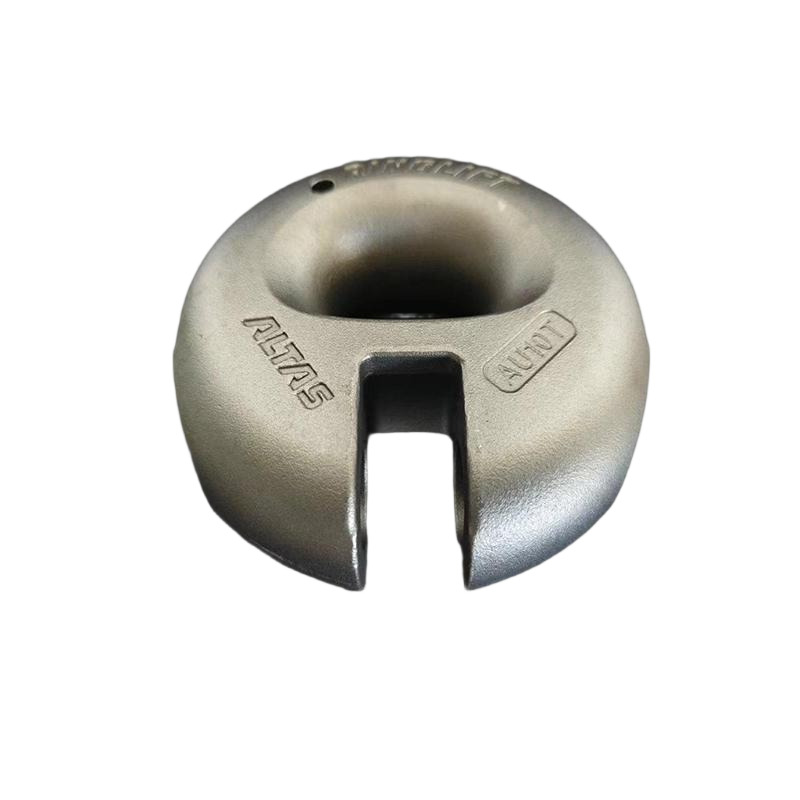
Duck-billed buckle, special sling for round-head sling
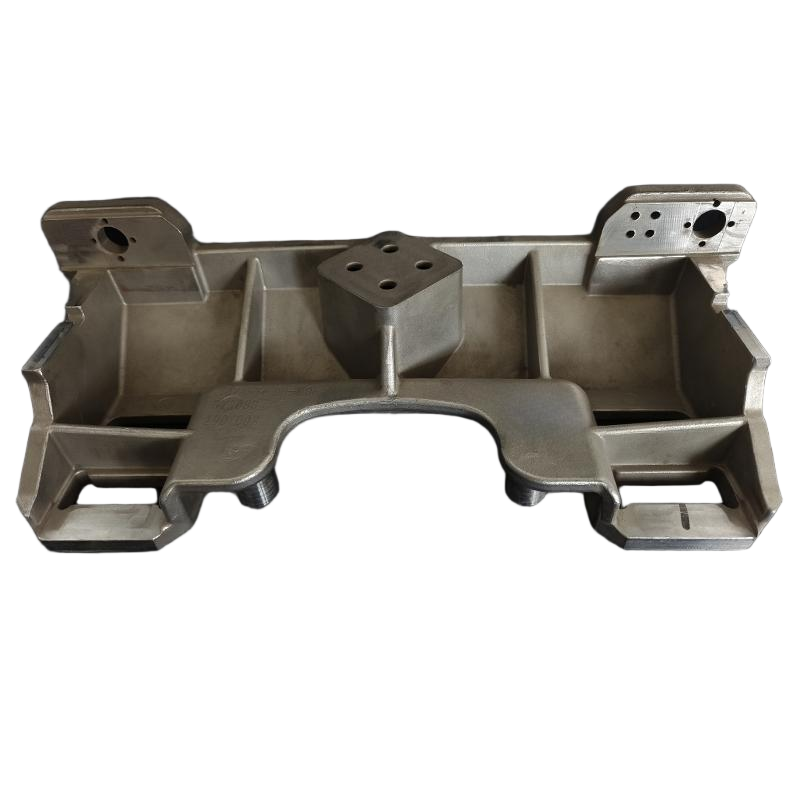
Precision casting in the field of ship safety
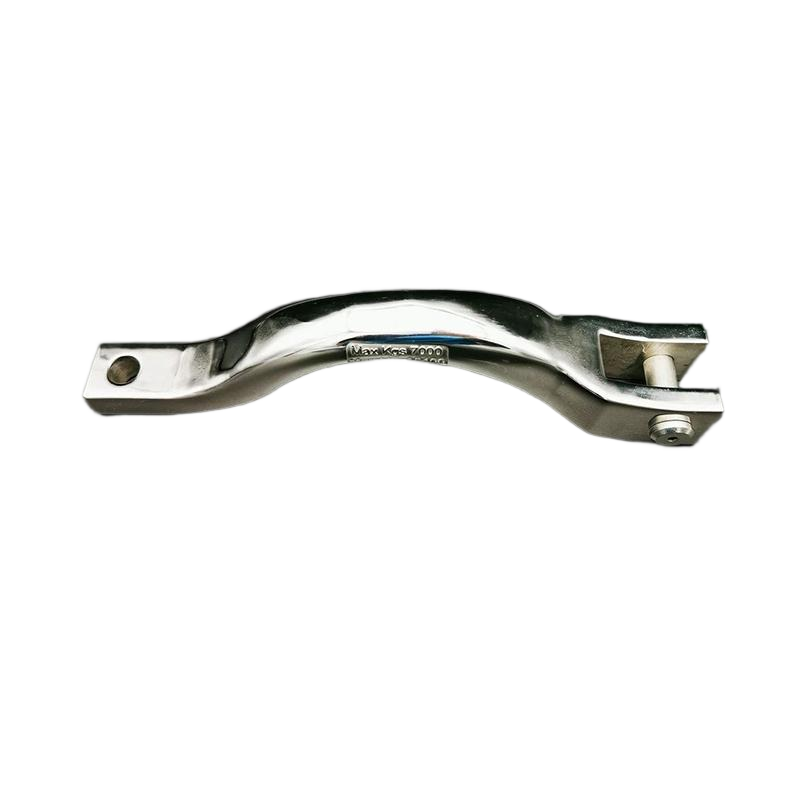
Precision casting in the field of ship safety
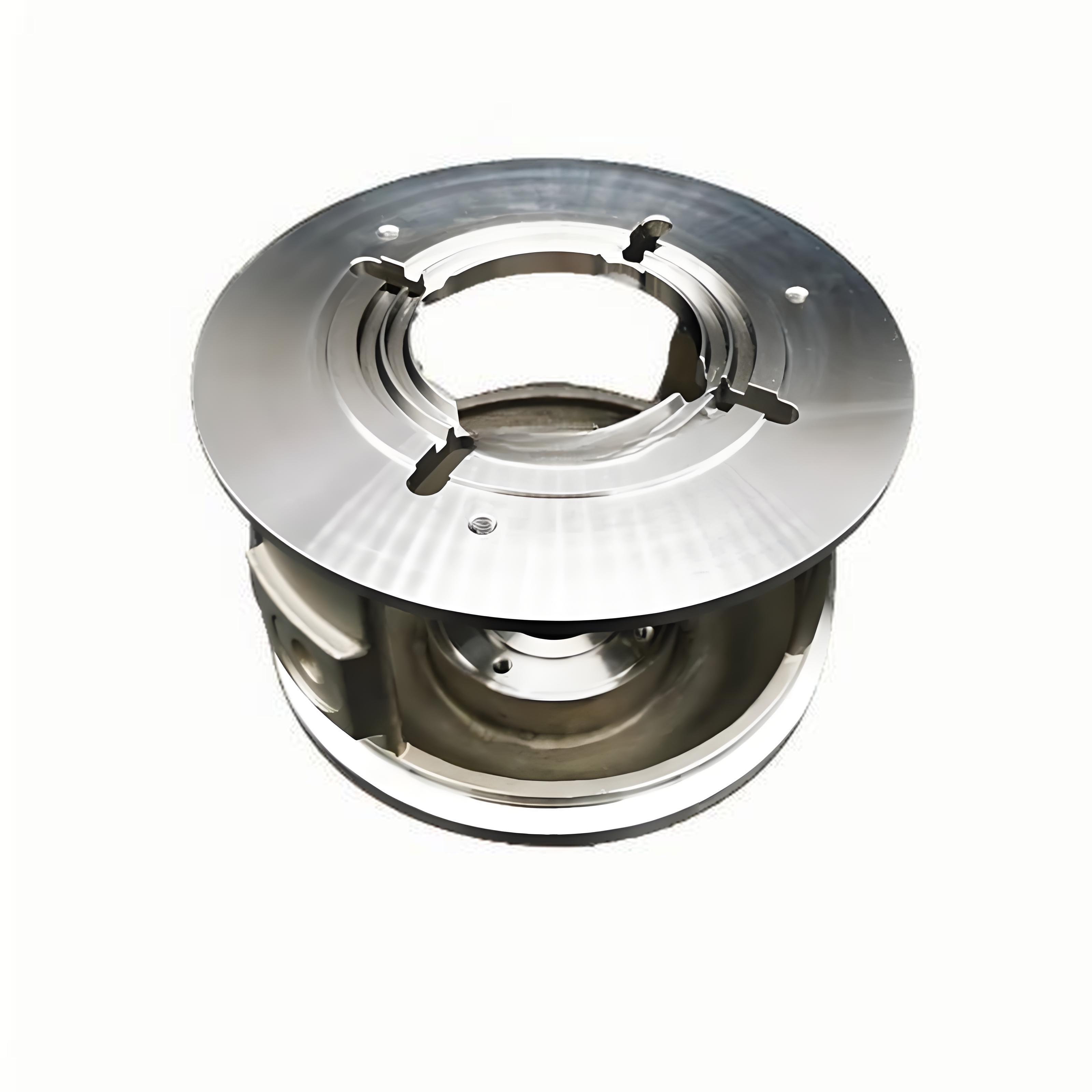
Precision casting in the field of ship safety
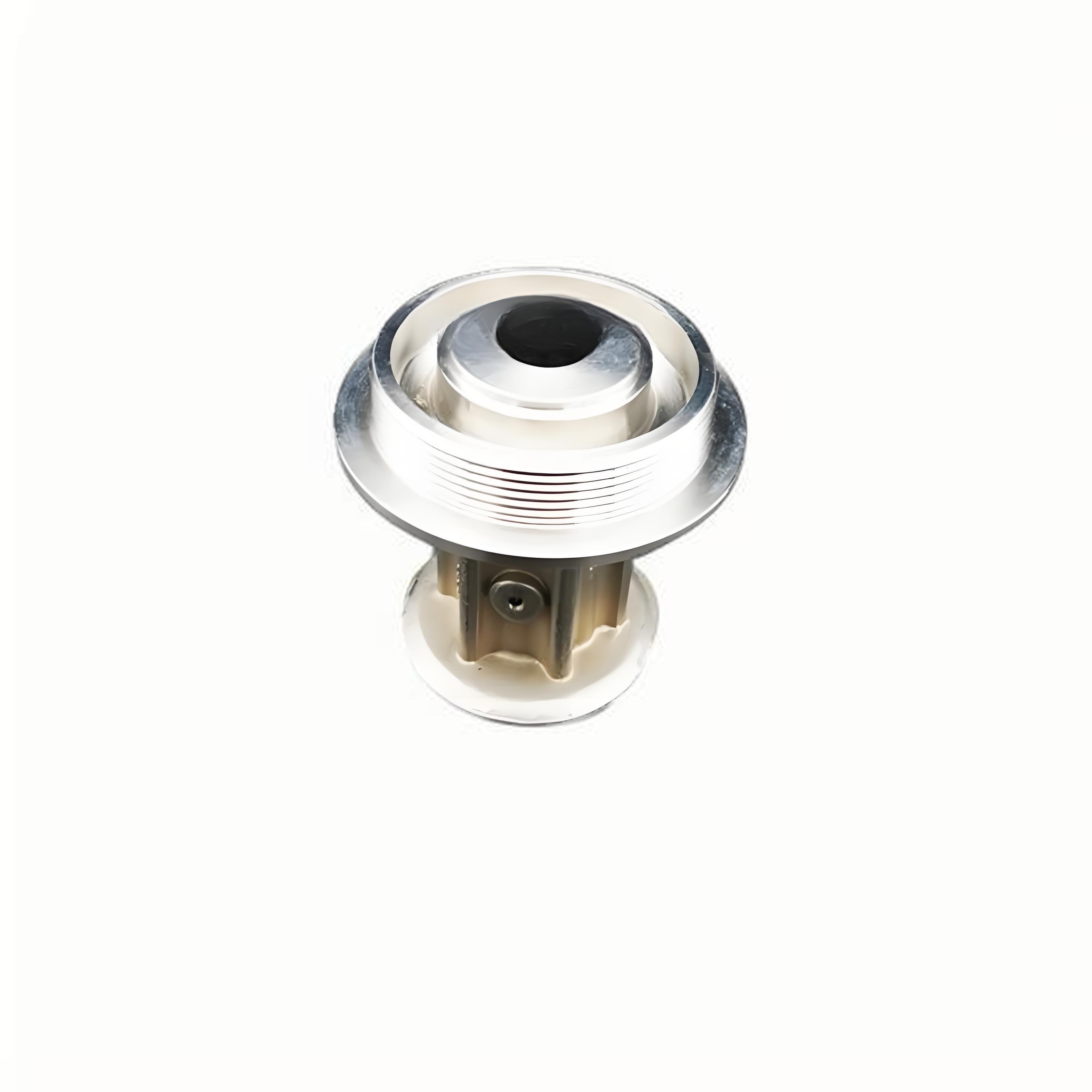
Precision casting in the field of ship safety
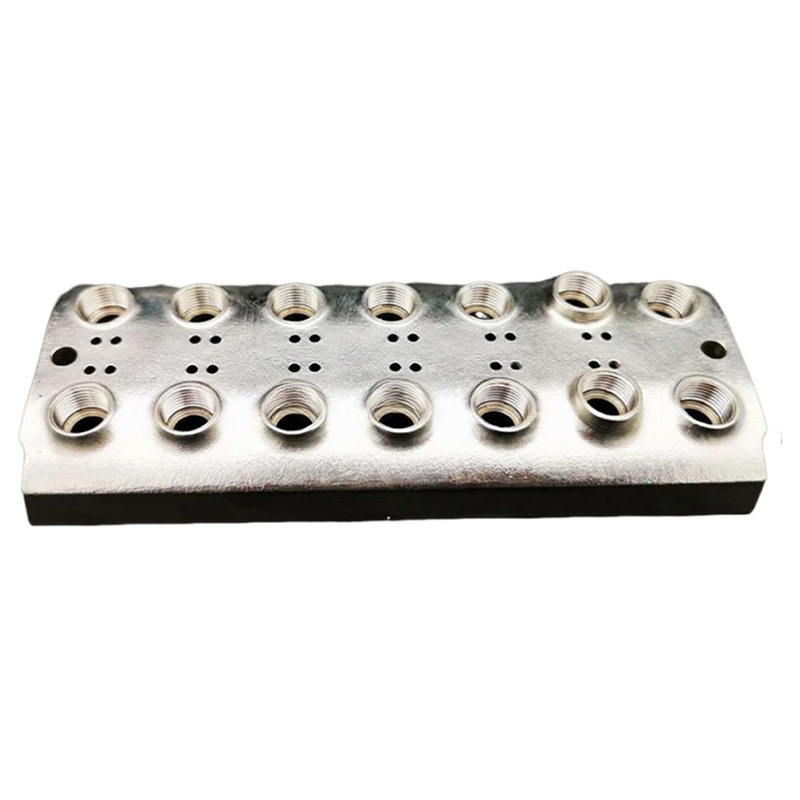
Precision casting in the field of ship safety
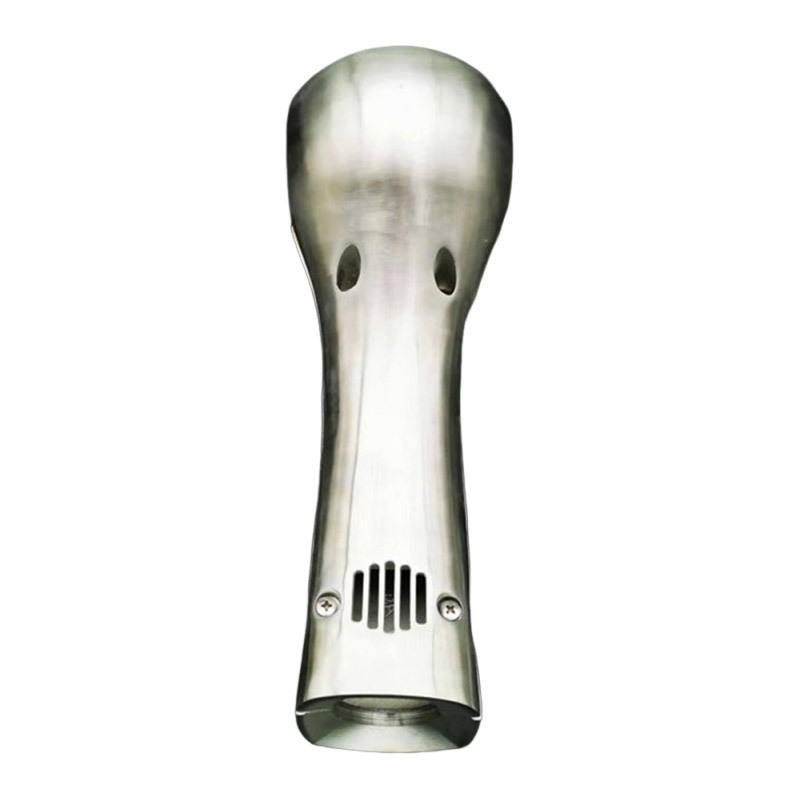
Precision casting in the field of ship safety
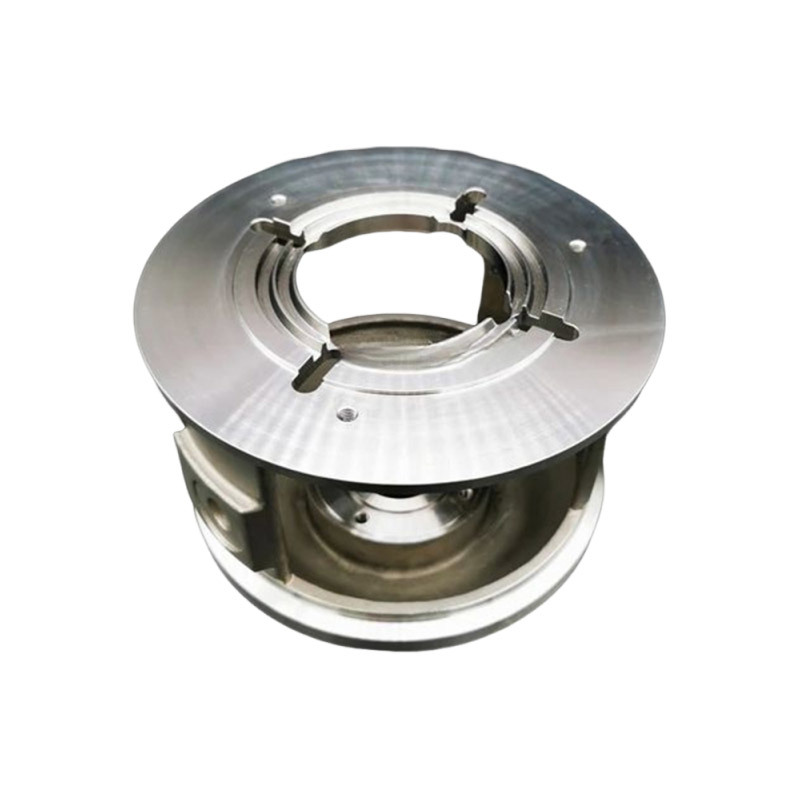
Precision casting in the field of ship safety